How Climate Change and COVID-19 Are Combining to Rock Renewable Energy Supply Chains
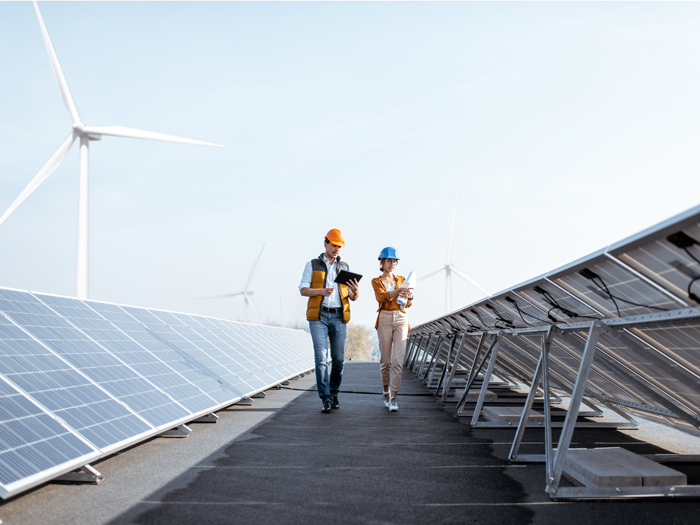
As baseball-sized hail fell from the sky, West Texas residents took cover. The rock-hard ice dented cars, smashed windows, and damaged property. The unmerciful May 2019 storm hit renewable energy too, damaging 13,000 solar panels and causing $70-$80 million in insured losses.
Approximately 16 weeks later, the solar panels were fixed or replaced and the site was up-and-running again.
If the same storm hit today, there’s no telling how long the damage might linger. Renewable energy supply chains have become increasingly tight due to a combination of equipment stockpiling, obsolete equipment and manufacturers inundated with new order requests.
Then came a global pandemic.
The supply chain situation has solar and wind companies holding their collective breath, hoping Mother Nature offers a gentle hurricane season and somehow limits lightning, wind, tornados, and hail.
“Another natural catastrophe or big hailstorm is absolutely the fear right now,” said Fraser McLachlan, CEO of GCube Insurance Services, a specialist provider for utility-scale renewable energy projects.
“Every three years or so, we’ve seen pretty significant claims due to high winds, wind-driven water, or flooding in the lower lying regions. If that happens again this year, it would cause significant problems in replacing a lot of that equipment.”
COVID-19 caused further disruptions, as lockdown measures and construction delays led to fewer wind turbines, solar plants, and other renewable electricity installations, according to the International Energy Agency. As a result, the world is set to add 13% less renewable power in 2020 compared to 2019.
“Countries are continuing to build new wind turbines and solar plants, but at a much slower pace,” said Dr. Fatih Birol, IEA executive director, in a statement.
“Even before the COVID-19 pandemic struck, the world needed to significantly accelerate the deployment of renewables to have a chance of meeting its energy and climate goals.”
The Rise of Renewables Gets Stricken With COVID
Solar, wind and other renewables have been powering the world for years, expanding access to developing nations and reducing pollution. Meanwhile, innovations are reducing costs considerably. As a result, the number of people without access to electricity fell from 1.2 billion in 2010 to 789 million in 2018, the IEA reported. The organization forecasts that the world’s total renewable-based power capacity will grow by 50% by 2024.
In the United States, renewable power has increased 100% since 2000 and represents the fastest-growing energy source in the United States, according to the Center for Climate and Energy Solutions. Renewables made up more than 17 percent of net U.S. electricity generation in 2018.
“Solar effectively shut down for a period of months in terms of supply chain.” — Fraser McLachlan, CEO, GCube Insurance Services
Then COVID-19 slowed supply chains. For wind, spare parts like blades, gear boxes, and generators have been delayed — ultimately slowing down projects.
“Pretty much every offshore wind construction project we’re involved with at the moment has been extended,” said McLachlan.
The pandemic hurt solar too, delaying the production and distribution of panels, inverters, and mounting equipment.
“Solar effectively shut down for a period of months in terms of supply chain,” said McLachlan.
Tax Credit Stockpiling and Obsolete Parts
COVID-19 is not the only factor squeezing renewable energy supply chains. Another is the Production Tax Credit, which provides per-kilowatt-hour tax credits for renewable electricity generation. The deadline led to energy companies stockpiling equipment — much like consumers feverishly bought toilet paper and paper towels in the early days of COVID-19.
But that stockpiling should mean that renewable companies can easily replace equipment if a natural catastrophe or other incident caused damage. Right? That depends, said Al Caceres, executive director of the energy practice at Gallagher. He agrees that “there is a lot of equipment in storage and ready to go” but says that the equipment goes obsolete quickly as manufacturers consistently refine and upgrade their products.
“There is a very fine line when it comes to replacing equipment,” said Caceres.
“When you buy an iPhone 11 and think you’re going to put an iPhone 9 case on it, it doesn’t fit.”
McLachlan agrees, saying that solar panels particularly go obsolete quickly.
“You almost have to redesign and remanufacture your entire project to suit the latest generation of panels that has come along,” said McLachlan. “That can happen in a two-to-three-year timeframe.”
If a solar company needs replacement equipment, expect long wait times and high prices. Caceres recalls a client who approached 10 solar panels manufacturers recently.
“Eight companies said ‘no’ right off the bat. That’s unheard of,” he said.
“Because companies are stockpiling solar equipment, equipment manufacturers were backlogged in trying to meet demands. The two companies that said yes raised prices more than 40%.”
Assessing Risk
Any supply chain conversation starts with a risk assessment by insurers and renewable energy companies. Ian Robb, head of global risk engineering for Liberty Specialty Markets, helps companies assess whether manufacturers far down the supply chain are reliable.
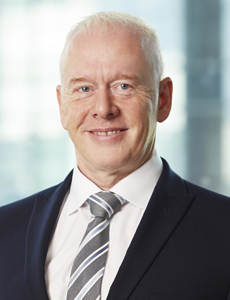
Paul Houston, head of risk management, global markets, Allied World
“The scale of renewable energy projects is becoming bigger and bigger. Insurers need some reassurance that the capacity to make even larger machines is conducted in a proper and qualified way, whilst maintaining equipment quality and reliability” said Robb.
“We also examine if they’ve performed contingency planning and identified where they can acquire similar equipment if original equipment manufacturers can’t supply them. It’s part of a whole contingency planning analysis.”
Logistics and transportation are also major concerns. Take wind energy, for example. Turbines can be 40-90 meters long and weigh nearly 100 tons. Getting such massive parts to their destinations takes carefully coordinated shipping logistics, powerful cranes, and heavy load bearing trucks. Then weather can disrupt it all, said Paul Houston, head of risk management, global markets for Allied World.
“Just a couple months ago, we had blades going from China to Australia, and a couple days into the voyage a typhoon hit, so we had to redirect the ship to safe port, stay there for a few days, then send it on its way to Australia,” said Houston
Then it takes several trucks and lots of sophisticated logistical maneuvers to transport wind turbines to their final destination. Houston has worked with teams that reroute electrical wiring, cut down trees, and reinforce bridges to clear a path.
“Wind farms are likely to be in quite a remote area, and it’s likely that the bridges and infrastructure leading up to it haven’t had anything that long or that heavy travel over them before, so we have to make sure the actual route is properly surveyed from start to finish so it arrives there safely,” said Houston.
A More Resilient Supply Chain
From COVID-19 to manufacturing delays to logistics, any supply chain issue in renewable energy underscores the importance of understanding supply chains and possibly bringing them closer to the point of sale.
“Companies don’t always know their supply chain. They don’t always know where they’re getting their goods from. They might think they’re getting a turbine from Denmark but actually the component parts come from China, Vietnam and Brazil,” said Houston.
“Companies are now trying to get their supplies closer to the point of sale. So instead of getting all your equipment from China, you might want to diversify it and get it from India and Brazil too, so if something goes wrong you can still keep up your manufacturing process. It might be more expensive, but it makes the supply chain more resilient.” &