From Talent Shortages to Climate Risks, Are Supply Chain Disruptions the New Normal?
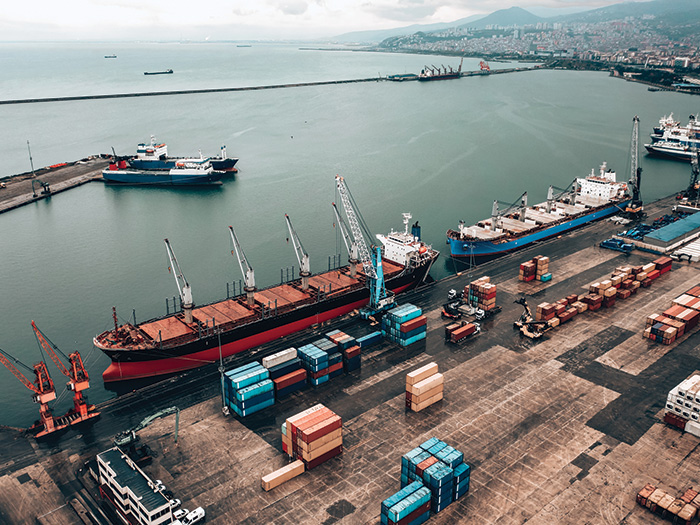
Dan Fegel remembers looking out at Los Angeles’ harbors in 2020 and seeing cargo ship after cargo ship waiting to get into port.
It was a stark contrast to what he was used to seeing. Before the pandemic disrupted global shipping patterns, boats used to come and go in the busy port. The Port of Los Angeles and the nearby Port of Long Beach handle 40% of the nation’s imports and exports. When the pandemic hit, “the only thing that you really saw running was the fuel ships going out to refuel,” said Fegel, who is national manager of risk management and loss control services for PCF Insurance Services.
Though many people resumed normal travel and activities after the government started widely distributing COVID-19 vaccines in 2021, it took shipping backlogs much longer to catch up. The Port of Los Angeles and Port of Long Beach backlogs didn’t ease until November 2022.
“There were many companies that had a contingency plan in place, but then when the pandemic hit and they pulled it out to look at it, they found that maybe some of those contingent suppliers weren’t even supplying the products that they needed anymore,” said Jon Meyer, advanced manufacturing practice lead, Travelers.
Shipping backlogs are one of several factors that created supply chain shortages in 2020. Panic buying, labor shortages and other pandemic-related factors strained supply chains. Then, a container ship lodged itself in the Suez Canal. Geopolitical conflict, increasingly frequent and strong storms and other factors have contributed to continued supply chain disruption in recent years, causing many to question whether disruption is here to stay.
COVID’s Lingering Consequences
Many point to the pandemic as the beginning of the supply chain woes companies have faced in recent years, but the potential for disruption began much earlier than that.
As Amazon Prime and other speedy delivery services hooked consumers on two-day and even next-day delivery, companies began relying on just-in-time delivery and maximizing their supply chains for efficiency, rather than building in redundancies. That made businesses incredibly susceptible to massive supply chain challenges.
“Relying on a just-in-time philosophy for delivery of goods and services is not going to be a winning long-term solution for most businesses. Redundancy, or at least a backup plan of some sort, has to exist prior to the event,” said Tracey Sharis, head of programs, Liberty Mutual’s North America Specialty/Ironshore division.
Today, experts are divided on whether the supply chain challenges that started during the pandemic have abated. Some are still feeling continued strain. “There is still a significant amount of supply chain disruption that we’re seeing even post-COVID,” Meyer said.
Others see it as a one-off issue for distinct sectors or businesses: “There is currently very minimal disruption in the supply chain other than individual situations,” said Chris Demetroulis, leader of Gallagher’s transportation practice.
“We’re not seeing the same impacts that we experienced during the pandemic, but the underlying risk has not gone away — in fact, it’s only shifting,” added Randal Waters, senior vice president of the emerging risks group at Marsh.
Regardless, the pandemic did shift supply chain risk in fundamental ways. Remember all the ships stuck in California’s ports? While they were sitting on the water, they became a ripe target for thieves.
“There was a ton of freight sitting, whether it was offshore outside the ports waiting to be offloaded or was offloaded from the ships and was sitting just outside the ports and drop yards, distribution yards,” said Scott Cornell, transportation lead and crime and theft specialist at Travelers. “Freight at rest is freight at risk.”
Cornell cites CargoNet data that found there was a 57% increase in cargo theft in the U.S. between 2022 and 2023. In the first quarter of 2024, there were 38% more thefts than there were in the same period of 2023, according to the cargo security company Overhaul.
“Cargo theft is something that has always been a top-three cause of loss in the transportation industry for the entire 29 years that I’ve been around,” Cornell said. “Over the past three years, it’s exploded in the United States.”
Another issue: Talent shortages due to the Great Resignation and baby boomer retirements can lead to production delays for a variety of goods. The pandemic spurred many to leave their jobs. Worker illness kept people off manufacturing lines. New workers are more likely to experience injuries: Travelers’ 2024 Injury Impact Report found 35% of all workers’ compensation claims come from employees in their first year on the job.
“So many manufacturers have existing employees with specialized skills who cannot be easily replaced, especially given the tightened labor market,” Meyer said. “Let’s say two people in your warehouse [are] injured because of an accident. All of a sudden, your ability to get your product to your customers becomes a little bit strained.”
Geopolitical Risk + Climate Catastrophe
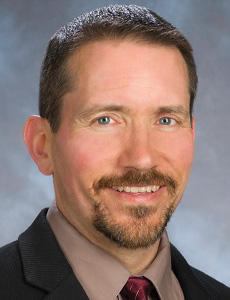
Scott Cornell, transportation lead, crime and theft specialist, Travelers
The continued impacts of COVID aren’t the only forces fatiguing supply chains, however. Geopolitical conflicts and persistent natural catastrophes are also burdening trade lines.
Let’s start with the war in Ukraine: The violence in the region has made it challenging for products to make it into and out of the country. If a business relied on fuel or goods supplied by Russia or Ukraine to do business, then they may have struggled to find new suppliers as war in the region shut down supply chains.
“In the U.S., many of our energy resources, such as fuel, as well as certain crops, such as grain and corn, come from Russia and Ukraine,” said Harish Kapur, CEO, Across America Insurance Services. “The current conflict between the two countries is making it difficult for those products to get to the U.S. and elsewhere, causing the price of these items to rise.”
Then let’s consider the effects of climate risk. As Fegel and I talked, he said, “Here in Utah, you can’t see the mountains because of all the smoke and added that “it seems every July and every August, we’re seeing far more forest fires.”
Climate change is making natural disasters like wildfires and hurricanes more frequent. These natural catastrophes can destroy factories, disrupt transportation and otherwise make it difficult to move goods from one place to another.
“Freight at rest is freight at risk.” — Scott Cornell, transportation lead, crime and theft specialist, Travelers
“The challenge confronting most companies is their supply chain can be composed of several suppliers spread across the world. And a growing number of those suppliers are increasingly exposed to the impacts of climate change in one or more of their locations,” said Marc Dantuono, senior vice president, director, head of property, MSIG USA.
It’s not just major weather events causing issues, either. Droughts can lower water levels in major shipping corridors, making it impossible for large container ships to move through. This January, Gatún Lake, which feeds the Panama Canal, had water levels six feet lower than they were in January 2023, Woodwell Climate Research Center found. That’s the lowest they’ve been in any January on record.
“The Panama Canal now limits the number of ships allowed through at certain times due to low water levels, causing longer wait times for the goods transported by those ships,” Kapur said.
A New Era of Supply Chain Risk Management
Continued supply chain exposures have many businesses considering how they can increase their risk management efforts.
“Businesses must now take an all-hazards approach to supply chain risk management. Rather than developing contingent supply risk management plans based on specific natural or manmade perils, companies must plan for the effects of the disruption — regardless of its nature or origin,” said Bob Perlman, area executive vice president, business continuity and resilience, Gallagher.
“Whether it’s a geopolitical issue or a weather event, if you have to change shipping lanes, that can cause a delay,” Cornell added. “Every adjustment, every issue can cause delays or changes.”
Many are starting by scrutinizing their supply chains, looking for gaps or backups should a region be vulnerable to climate or geopolitical risks.
“If you’re getting all of your parts or components from one country or one place on the globe, and if it’s the only place you can get them, then that’s a known risk,” Demetroulis said.
One way companies are tackling supply chain risks is by using new technologies to map their exposures and vulnerabilities. Companies are starting to use internet of things (IoT) technology to track objects in transit and create live maps of supply chain exposures.
“We’ve heard, ‘We have a complex supply chain with so much to keep track of that a live platform is the only way to manage it,’ ” Waters said. “Now is not the time to be complacent. Rather, it’s the time to invest in the tools and capabilities that build resilience.”
“The internet of things is providing real-time visibility into all operations along the supply chain, boosting transparency and thus enabling quicker response times,” Dantuono added.
Others are mitigating risks by moving their suppliers closer to home. Onshoring and nearshoring the supply chain — which means moving the supply chain closer to home — has accelerated in recent years, a Gallagher report found. So a U.S. company might move from using suppliers in Asia to relying on ones in Mexico or Canada.
“Given current geopolitical tensions as well as extreme weather, many companies now recognize a need to develop a more strategic approach to supply chain risk management. This includes identifying alternate sites or suppliers in Asia, nearshoring and even onshoring. This is particularly relevant with companies with long and complex supply chains,” Perlman said.
On the whole, COVID’s supply chain disruptions taught businesses to be more proactive about managing supply chain risks, and that helped minimize the impacts that events like the war in Ukraine or climate challenges can have on the system.
“With visibility, a small amount of prevention goes a long way to minimize impacts,” Waters said. “There’s a fundamental need to understand risks quantitatively and holistically.”&