Why the Urgent Need for Virtual Risk Assessment Will Never Eclipse Boots-on-the-Ground Expertise
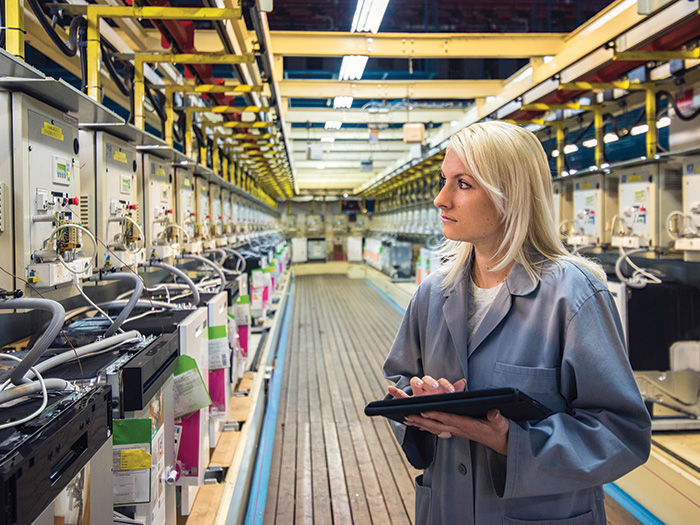
At a large food production plant in Nicaragua, an employee methodically guided a Zurich risk engineer through the facility. They examined heavy equipment, storage operations, and fire prevention systems. The engineer asked pointed questions about potential risks and shared ways to make the plant safer.
But the engineer did not visit in person. Instead, he watched a video feed shot on a cellphone, and used software to annotate images and videos. He also wasn’t alone — engineers in Mexico and Switzerland joined too. So did a company representative in Panama.
They didn’t have to get on airplanes. They didn’t have to risk contracting COVID-19. But they still ended up with a robust picture of potential risks and placed coverage accordingly.
Welcome to risk engineering in the age of a pandemic.
Global travel restrictions and safety policies slowed on-site risk assessments considerably. When engineers could no longer visit facilities in person, they did the next best thing — touring facilities virtually, scouring available data about potential risks, and using cutting-edge software to help keep track of their findings. Many other industries used remote meeting technology during the pandemic, and risk engineers were no exception.
Pandemic or not, business needs to continue, and insurance coverage needs to be placed — even if engineers can’t physically walk through large, complex facilities like hotels, power plants or oil refineries. Experts believe the remote risk engineering approach is working well and expect aspects of it to continue after the pandemic.
But they agree that it’s no replacement for an in-person engineer who can use their eyes, ears, and nose to uncover potential problems.
The Rise of Remote Risk Engineering
With approximately 800 people conducting risk assessments in more than 40 countries, Zurich developed remote risk engineering technology before the pandemic but only used it sparsely. COVID-19 led to a 10x increase, said Fausto Steidle, Zurich’s head of risk engineering operations.
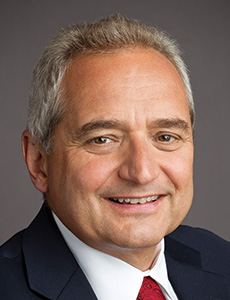
Brion Callori, senior vice president of engineering and research, FM Global
“The uptick was really extreme,” said Steidle. “When the pandemic hit in March there was no other option.”
Thankfully, employees everywhere were getting acclimated with Zoom, Microsoft Teams and other online meeting tools — so virtual risk assessments felt natural. The Zurich team used the technology to focus on relationships. Each Zurich remote assessment starts with a conversation — just like it would in real life. Developing a rapport face-to-face (or at least screen-to-screen) is crucial.
“Building that rapport with the customer, looking them straight in the eyes, getting that commitment to jointly wanting to improve the risk is key,” Steidle said. “Our people are technically excellent but they’re also quite good at building rapport with clients. Risk engineers have more face-to-face time with our customers than any other part of the business.”
Remote risk assessments can be more effective than not visiting at all. That proved true when Zurich was asked to quote a 31-story mixed use building in Dallas. With an underwriter virtually examining critical locations like communal areas, power generator and fire prevention systems, Zurich estimated the maximum loss at $14 million. If that underwriter had relied solely on research, it would have been estimated at $400 million, according to Steidle.
“That’s a really good example of how quoting blind on a piece of business leads us to think about the worst scenario and could have priced us out,” he said. “But because the remote process showed the underwriter the risk, we were able to get a clearer picture of the risk and provide a more competitive quote.”
Paragon is another company that turned to remote risk engineering. Pre-pandemic, it conducted approximately 10% of its assessments remotely but developed a solid remote approach after dealing with travel restrictions due to Australian wildfires and other man-made and natural catastrophes. That served the company well during COVID-19, as it conducted as many as 90% of its business remotely during the height of travel restrictions.
A major challenge was uncertainty, particularly in the early days of the pandemic.
“The biggest challenge was trying to understand the rules at different times in different regions, countries or states,” said Rob McMullen, president of Paragon Risk Engineering. “Our response was very regional, sometimes specific to a certain province in one country.”
McMullen shared the story of a large organization they’d been dealing with for a decade. Engineers examined the facility previously, so they decided to take a different tact when forced into remote engineering. They took a deep dive into testing and inspection records — finding that tests on combustible dust and electrostatic equipment were not done properly or frequently enough.
“Would we have come across that over the next few years doing traditional surveys? Maybe, maybe not. That’s an impossible question to ask. But we know for 100% fact that discovering that problem was due to that super deep dive into their records which we would not have done in the near term with a traditional approach,” he said. “After the pandemic, we’re not going to lose that discipline, we’ll keep doing it.”
Lessons Learned: Screen Fatigue, Hidden Risks
FM Global engineers conducted 49,000 site visits in 2020 — of which 15,000 were remote, according to Brion Callori, senior vice president of engineering and research. One lesson Callori and his team learned right away — preparation is key. Collecting data, and dutifully preparing questions helps make the process more efficient.
“We collect 700 to 1,200 pieces of data on every location we visit,” said Callori.
FM Global also realized that remote engineering takes time. Having team members methodically walk through every corner of a facility with a smartphone camera while answering pointed questions can take longer than traveling there in person.
“You’ve got to break tasks down into manageable chunks or your clients could start to get fatigued,” said Callori.
Expect remote risk engineering at FM Global to continue after the pandemic. In three years, the company hopes to collect 60% of all data before an engineer gets on site, and it plans to allow subject matter experts to virtually join on-site risk assessments.
“We hope it’s more efficient and we have to travel with specialists less,” he said. “If the engineer has a challenging exposure they need help on, they can call the subject matter expert on the app. Right away it’s going to be a lot easier.”
Boots-on-the-Ground and the Future of Remote Risk Engineering
Experts agree that remote risk engineering cannot replace in-person assessments. They miss the casual conversations with rank-and-file employees like a forklift driver or machine operator. They don’t allow an engineer to see, hear, and touch things — asking questions on the fly like “what’s behind that door?” or “why is that stored there?”
“The limitations ultimately outweigh the benefits,” said McMullen from Paragon. “There have been a few things that have helped our company refine our discipline and hone our depth of understanding about certain topics but the simple fact is — you will physically miss things when you’re not there walking around.”
FM Global’s Callori agrees.
“You can’t replace that assessment and mitigation of loss and do it totally remotely. It’s about those degreed engineers who have been specifically trained getting their eyeballs on site, walking around, getting a feel for the facility, and really building that consulting relationship with local clients,” Callori said.
Mike Rendich, vice president of North America Risk Control and General Property at Berkshire Hathaway Specialty Insurance — who spent many years conducting risk assessment surveys — doesn’t think remote risk engineering will totally replace in-person site visits.
“There are a lot of things you don’t know until you see them, and you’re not going to see them in a virtual survey,” Rendich said.
Of course, streaming video is better than nothing, Rendich noted, but it has limitations.
“You will only see what’s in the frame, not the 360 view you get when walking around, looking up, down and all around,” said Rendich.
If remote engineering is not as good, it begs the question — are we one catastrophe away from disaster?
“There hasn’t been a traditional large industrial fire that’s impacted the commercial insurance sector since the pandemic. You can be sure that if one happens in early 2021, everybody will be saying that terms and conditions will be limited or curtained based off of accurate risk information from offsite risk engineers,” McMullen said.
Without human risk assessments, underwriting decisions can be a judgement call.
“It’s not black-and-white. We just have to use judgement,” Callori said. “Has this process given us enough information to allow us to properly assess and underwrite the risk?”
Steidle agrees: “Zurich has hundreds of thousands of customers and risk engineering sees a small amount of them, so we are writing a lot of business without any risk engineering input. The underwriter has to go with the best information available, and that could mean we’re a bit more cautious.” &