2016 Teddy Awards: Honorable Mention
Keeping the Results Flowing
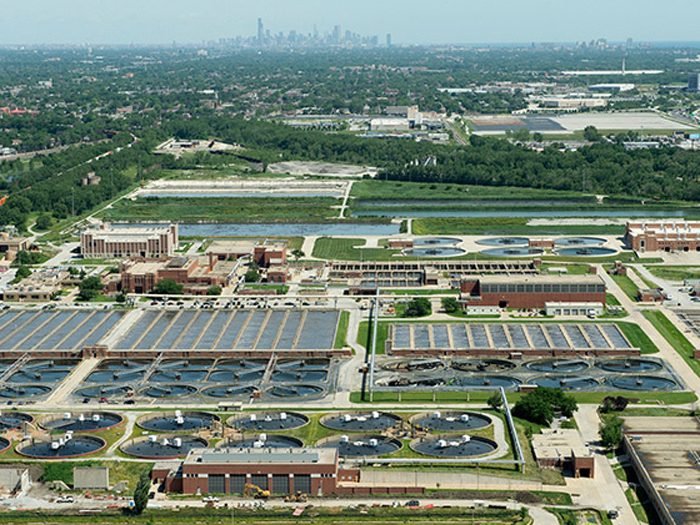
The mission of the Metropolitan Water Reclamation District of Greater Chicago (MWRD) is to protect the health and safety of citizens and of area waterways throughout Cook County, Illinois. In order to do that, the agency must first protect the health and safety of its nearly 2,000 employees.
The MWRD serves the City of Chicago and 125 suburban communities. It operates one of the largest wastewater treatment facilities in the world, in addition to six other plants and 23 pumping stations that provide treatment for residential and industrial wastewater.
The MWRD is also responsible for stormwater management. In fact, the MWRD’s Tunnel and Reservoir Plan (TARP) is one of the country’s largest public works projects for pollution and flood control. TARP’s four tunnel systems total 109 miles of tunnels, 9 to 33 feet in diameter and 150 to 300 feet underground. Two reservoirs are in operation, and construction is in progress on the third and final reservoir.
With the absolute goal of sending all workers home safely at the end of the workday, the MWRD has invested a great amount of time assessing the risks its workers face and how to best address them. Most of the facilities are heavy industrial environments, and many of the jobs require substantial physical labor.
Job duties vary significantly, from trade specific roles to those of general laborers, whose tasks are often driven by the immediate needs of the day. Adding to the dynamic is that employees tend to stay with the MWRD for a long time; the average age of the workforce is over 50.
The MWRD’s robust eLearning program incorporates 200 trades-based and industry-based courses, in addition to offering general business and computer training.
The MWRD has implemented a variety of loss control strategies to reduce both the number and the severity of injuries on the job. For instance, the MWRD now provides dipolar (bifocal) safety glasses with 2x and 3x magnification for tradespeople who are doing close up work in order to accommodate changes in eyesight.
Additional chain falls were added so pipefitters would not have to bend over to lift lengths of pipe. Mechanized turntables for garbage dumpsters have been added to minimize manual raking and poor ergonomics. A strong emphasis is placed on using two-person lifts, and extra carts were provided for moving tools from place to place. These initiatives reduce the likelihood and impact of strains and back injuries.
Given the importance of back safety, the MWRD engages outside experts bi-annually to deliver dozens of back safety and body mechanics classes. In-house safety staff conduct training as well. In 2015 alone, MWRD safety staff conducted 498 training sessions for 7,122 employees on 53 different topics, prioritizing key activities and key areas of injury.
eLearning Central
The MWRD also strengthened its return-to-work program to ensure injured workers remain engaged throughout their recovery process and return to employment as soon as they can do so safely. Many jobs at the MWRD are highly physical, so light duty options are not always available or appropriate.
A transitional duty option – eLearning – was incorporated to accommodate medical releases to sedentary duty. The MWRD’s robust eLearning program incorporates 200 trades-based and industry-based courses, in addition to offering general business and computer training. eLearning is now a central component in the MWRD’s return-to-work strategy.
The MWRD’s approach to medical management is holistic. A number of steps have been taken to mitigate the cost and impact of injuries. Local clinics are designated for each plant and are briefed on MWRD jobs and protocols as well as the return-to-work program.
At the largest plant, the MWRD contracts with a physical therapy provider who treats injured workers on-site so employees do not need to leave the premises. The medical case management system uses outside nurse case managers to work with the injured worker, our third party claims administrator, and doctors to assure that the injured worker is receiving appropriate treatment on a timely basis.
With a 360-degree focus encompassing injury prevention, return-to-work, and medical case management, the MWRD has experienced dramatic reductions in costs per claim, medical costs, and the number of lost time claims. As of October, the MWRD recorded 67 claims for 2016, a remarkable drop from the 150 recorded just five years ago for full year 2011.
“This has truly been a collaborative effort and has resulted in a cultural change around workers’ compensation within our organization,” said Ruth Joplin, MWRD Risk Manager. “Throughout the process, management support and supervisor engagement has been key. We are amazed and gratified to see what has been accomplished in such a short time.”
Risk & Insurance® is pleased to recognize the Metropolitan Water Reclamation District of Greater Chicago with a Teddy Award Honorable Mention. &
_______________________________________________________
Read more about the 2016 Teddy Award winners:
Bringing Focus to Broad Challenges: Target brings home a 2016 Teddy Award for serving as an advocate for its workers, pre- and post-injury, across each of its many operations.
The Road to Success: Accountability and collaboration turned Hampton Roads Transit’s legacy workers’ compensation program into a triumph.
Improve the Well-Being of Every Life: Excela Health changed the way it treated injuries and took a proactive approach to safety, drastically reducing workers’ comp claims and costs.
The Family That’s Safe Together: An unwavering commitment to zero lost time is just one way that Harder Mechanical Contractors protects the lives and livelihoods of its workers.
More coverage of the 2016 Teddy Awards:
Recognizing Excellence: The judges of the 2016 Teddy Awards reflect on what they learned, and on the value of awards programs in the workers’ comp space.
Fit for Duty: 2013 Teddy Winner Miami-Dade County Public Schools is managing comorbid risk factors by getting employees excited about healthy living.
Saving Time and Money: Applying Lean Six Sigma to its workers’ comp processes earned Atlantic Health a Teddy Award Honorable Mention.
Caring for the Caregivers: Adventist Health Central Valley Network is achieving stellar results by targeting its toughest challenges.
Advocating for Injured Workers: By helping employees navigate through the workers’ comp system, Cottage Health decreased lost work days by 80 percent.
A Matter of Trust: St. Luke’s workers’ comp program is built upon relationships and a commitment to care for those who care for patients.
Keeping the Results Flowing: R&I recognizes the Metropolitan Water Reclamation District of Greater Chicago for a commonsense approach that’s netting continuous improvement.