2014 Teddy Award Winner
Quick to Act
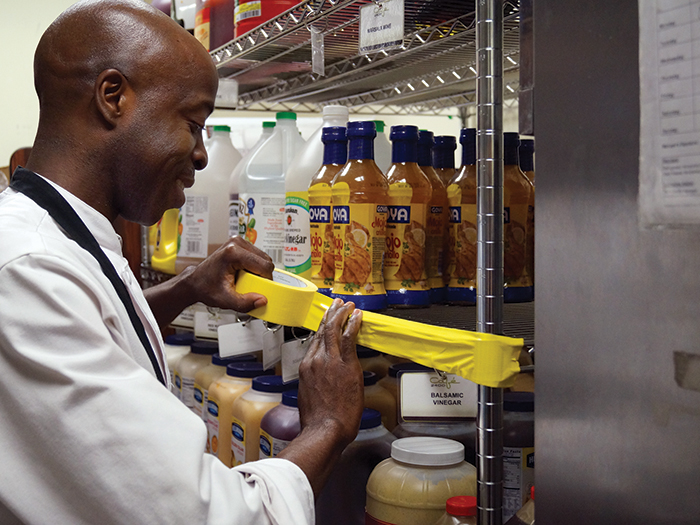
A housekeeper at Memorial Health Systems — part of the food service and support services company Compass Group North America — was hard at work mopping a patient’s room one day. He misstepped, and before anyone could react, he was down on the ground with an injured lower back, shoulder and wrist.
Normally, slip and falls of this kind — consistently one of the leading causes of injury affecting workers of all stripes — can keep an employee out of work for long periods of time.
Not in this case.
As usual, the employee received medical treatment and was given all of the following restrictions: No pushing. No pulling. No lifting more than five pounds, and no prolonged standing.
Fortunately, Compass Group — which boasts over 10,000 different locations across the country, offering corporate food services, facilities management, janitorial services, and more — had implemented an innovative return-to-work (RTW) program in early 2014.
That successful program and related safety initiatives are why the organization is one of the 2014 Theodore Roosevelt Workers’ Compensation and Disability Management Award winners.
The RTW initiative offers dozens of modified duties — tasks calling for minimal physical effort so that associates can get back to work in short order.
“A big part of the effort was to find different types of altered duty able to bring our associates back to work just as soon as possible — just not in their original capacity,” said Ron Ehrhardt, vice president of operational safety with Compass Group.
“They could be a cashier if not a grill cook,” in the food service units on a temporary basis, for instance, he said.
The housekeeper’s case presented a more difficult challenge, Ehrhardt said, since the Environmental Services Unit (EVS) at the worksite already had two employees on modified duty. With productivity strained, the organization was hard-pressed to provide modified duty for yet another worker.
Management was quick to act, however.
It identified a modified work opportunity with the company’s Patient Transport Division, another Compass Group business line, which includes companies such as Crothall Healthcare, Eurest Dining Services, Morrison Healthcare/Senior Living, TouchPoint, and Wolfgang Puck Catering and Events.
By moving the housekeeper and tasking him with administrative work in another unit, the company was able to maintain its productivity as well as return the man to work in an expedited fashion.
During subsequent doctor visits, the employee’s restrictions were expanded, to allow him to lift up to 15 pounds and engage in limited standing.
At the same time, one of the two employees in the EVS unit who’d previously been on modified duty was released to full duty, so management was able to move the housekeeper back to his home location to complete his modified duty roster.
The result: No loss of workdays for the injured worker or anyone else in the EVS unit.
Impressive Results
The proof of the pudding is in the eating, as they say.
“The policy we wrote on return-to-work was implemented in March,” Ehrhardt told Risk and Insurance®. And whereas Compass had been seeing a slight increase in out-of-work days prior to the new policy, the company has seen a 7 percent net improvement in this metric during the past fiscal year.
And unsurprisingly, thanks to a bonus structure which rewards Compass units that do not incur any injury claims in the course of a year, the company’s operating units are largely compensation claims free.
“A full 75 percent of our accounts had zero claims in the last fiscal year, 2014, which is just ending,” said Palmer Brown, chief corporate investment & risk officer with Compass Group NA.
The return-to-work program was initiated through collaboration between the company’s safety leadership team and its TPA, Gallagher Bassett.
As part of the initiative, Compass Group implemented a RTW coordinator program. Based on specific criteria (i.e., severity, injury type and work status), cases are assigned to a RTW coordinator, a registered nurse, or closed.
For less complex cases, a RTW coordinator is given the goal of managing the RTW process and monitoring each medical visit to ensure that an injured worker gets back to full duty. The coordinator’s role is to expedite this process and communicate all pertinent information to the employer and adjuster.
A nurse is assigned to more severe cases. Similar to the RTW coordinator, the nurse works with the adjuster to get the associate back to work.
Safe Storage
Compass Group also recently implemented a “safe storage” plan, designed to eliminate unsafe situations that result in poor ergonomic lifting positions in storage rooms, janitorial closets, supply rooms, and walk-in refrigerators, among other areas.
“No two storage areas are the same, so the safe stacking and storage plan are meant to be used as a guide” to mitigate or eliminate injuries caused by heavy lifting, Ehrhardt said.
“We looked at our loss data and some of our associates were clearly getting injured — not because they were doing anything wrong, but because they were grabbing for items stored at the wrong shelf height,” he said.
For example, the safe storage model for a four-shelf unit is as follows:
• Shelf No. 1 (The top shelf) should have lighter, lesser-used items, lighter than 20 lbs.;
• Shelf No. 2 (second from the top) can be used for heavier items, but should be used mainly for the most frequently used items;
• Shelf No. 3 (second from bottom) is to be used for the heaviest, bulky, and difficult to handle items. The shelf should be outlined in yellow tape or paint; to indicate caution while lifting a heavy item; and
• Shelf No. 4 (the bottom shelf) should store lighter, less frequently used items as well as items with handles, which have not been stored on the middle shelves due to the ease of grasping and position.
In addition, he said, employees were getting injured removing heavy bags out of trash receptacles. Previously, trash bags were as large as 55 gallons, with no airflows to ease the task of pulling trash up and out. Thus, Compass Group decided to go with smaller-size vented receptacles that eliminated suction by roughly 50 percent.
These initiatives were implemented over the course of this year and have received numerous positive comments from account managers for ease of implementation and reduction of injuries.
Mike Recker, executive director with broker Willis Ltd. in Birmingham, England, applauded the new safety practices — particularly Compass’ latest return-to-work initiatives.
“A big part of the effort was to find different types of altered duty able to bring our associates back to work just as soon as possible — just not in their original capacity.” — Ron Ehrhardt, vice president of operational safety, Compass Group
In the seven years that Willis has been Compass Group’s global insurance broker, he said, “the management of risk, and specifically the safety of employees, have ranked high on the agenda at each and every Compass Group PLC board meeting,” he said.
“Under Brown’s leadership, Compass Group NA has achieved a clearer understanding of its risk profile and its injury loss drivers,” Recker added.
“We have [also] seen a closer working relationship with stakeholders including Compass TPA Gallagher Bassett as well as Willis, with a greater focus not just on cost management but how that cost is expended to achieve better results for its associates,” he said.
“The return to work initiatives [Compass recently] implemented are prime examples of the kind of innovation that has been introduced,” said Recker.
“Clearly, having senior inspirational leadership who are out in the field working along associates and the importance of this kind of continued engagement will enable the continued development and deployment of still more fresh innovative ideas,” Recker said.
_______________________________________________________
Read more about all of the 2014 Teddy Award winners:
Building Value with Trust: Honda of South Carolina boosted its involvement with injured worker cases, making a positive first impression on employees and health care providers.
The TLC Behind the Roar: A proactive and holistic approach to employees’ well-being has resulted in huge reductions in work-related injury claims for Harley-Davidson.
Quick to Act: Compass Group is lauded for its safety initiatives and for a return-to-work program that incorporates all of its business lines.
Healing the Healers: Teddy Award winner Cold Spring Hills Center for Nursing and Rehabilitation proved that even small organizations can make a huge difference in their employees’ lives.