Supply Chain Risk
Harvey Hampers Third of U.S. Refining Capacity
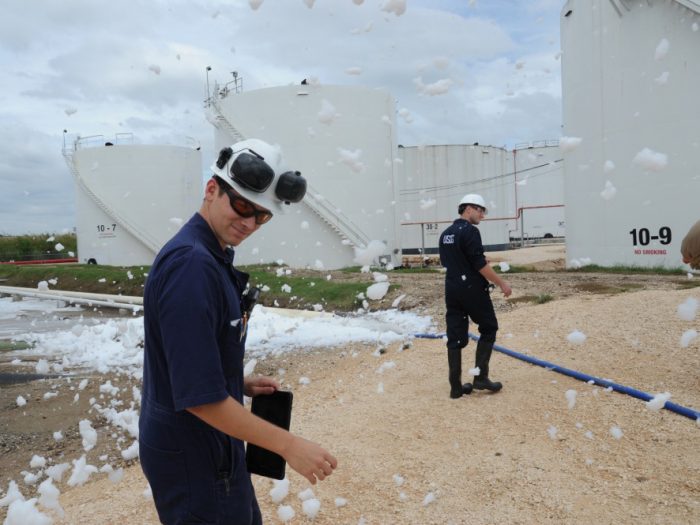
Coast Guard personnel walks through Aqueous Film Forming Foam (AFFF) as the top layer blows off spilled oil at a Kinder Morgan Liquid Terminal in Houston, Texas, Aug. 30, 2017. AFFF is a safety measure used to prevent exposed petroleum from igniting. Photo: U.S. Coast Guard
From the newest export terminals for liquefied natural gas to refineries first built before World War II, Hurricane Harvey’s track from Corpus Christi, Texas to Louisiana could not have been better designed to imperil the heart of North America’s refining and petrochemical industry.
The U.S. Department of Energy (DOE) reported that six refineries around Corpus, seven running from Houston to Galveston, and two more in Beaumont and Port Arthur shut down. Five others across the region were operating at reduced rates. Those closures comprise refining capacity of almost 4 million barrels per day.
That represents about 40 percent of total capacity along the Gulf Coast, and 21 percent of total U.S. refining capacity. The five refineries operating at reduced rates represent a further 1.5 million b/d, or 16 percent of Gulf Coast capacity and 8 percent of total U.S. capacity. That raises the total national capacity impinged to a stunning 29 percent. Beyond the processing capacity, at least 11 oil and gas pipelines were shut or operating at reduced rates either because of actual flooding or for lack of volume.
The Cambridge Centre for Risk Studies tracks the economic activity of 300 cities around the world assessing them for the implications of shocks and disruptions. According to Andrew Coburn, director of the advisory board, the core gross domestic product (GDP) for Houston is $314 billion. In January the center ran a model of a storm similar to Harvey hitting Houston and estimated that the total economic hit to that GDP at $60 billion. The GDP of the greater Houston area is about $500 billion. Proportionally that would put storm disruption at $100 billion.
“Beyond the immediate impact to industry,” said Coburn, “there is also the disruption to the national and global supply chains.” Houston is a major rail center, container port, crude-oil and fuels port, air hub, and trucking center.
Upstream of the refineries, oil and gas production offshore as well as in the prolific Eagle Ford shale formation in south Texas is heavily reduced. Jeff Quigley, director of energy markets for Stratas Advisors, said during an August 30 webinar that he expected offshore production to come back sooner rather than later. Onshore production, however, was harder to forecast because it is so decentralized.
“Beyond the immediate impact to industry, there is also the disruption to the national and global supply chains.” — Andrew Coburn, director, External Advisory Board, Cambridge Centre for Risk Studies
David Robertson, global head of energy risk consulting for Allianz estimated that about 800,000 b/d of oil production was impacted, which is close to 10 percent of the national total. “That is having a predictable impact on pricing.” He added that the pipelines and are under particular pressure.
Several insurance and process-industries sources noted that refineries and chemical plants along the Gulf Coast are designed to withstand hurricanes, and that operators had sufficient time to wind down operations and secure the facilities. However, pipe racks, pumps, and tanks are all vulnerable to leaking, floating, or being displaced by water or debris.
“The refineries are run by sharp people who have learned important lessons from previous hurricanes,” said Robertson. “They have a good track record for operations, especially at a steady state. Historically the largest losses in the industry have not come from storms but from incidents on start up, shut down, or maintenance.”
The notable exception to facilities being secured is the Arkema peroxide plant northeast of Houston in Crosby, Texas. When the plant was flooded and lost its generators, the peroxides could not be kept cooled and auto-ignited in a series of fires that caused toxic releases. Why that facility was more vulnerable than others to flooding has yet to be determined.
Other than that there have yet been no reports of major damage to industry as a result of the storm. “The waters are only just starting to go down but we have not heard of any significant damage to refineries or chemical plants,” said John A. Rathmell, Jr., president of Lockton marine and energy, and a former Risk & Insurance Power Broker.
“A lot of our clients in the energy and chemical sector have been through multiple storms. They have hardened their faculties by raising critical equipment off the ground. So far we have not heard of any problems with process unit integrity.”
Two other common concerns are pollution and business interruption (BI). The latter is not likely to apply broadly, Rathmell explained, because most of the major oil and chemical companies retain those risks. Those that do buy BI coverage may have 30- or 45-day waiting periods, more commonly 60- or 90-day.
Pollution liability is much more complicated, he added. Unless it can clearly be demonstrated that a substance leaked from a certain facility, then contamination is likely to be considered ambient in such a massive flood. Hundreds of gas stations, warehouses, junk yards, and dumps were inundated by Harvey.