How Poor Ergonomics and Musculoskeletal Disorders Lead to Opioid Deaths
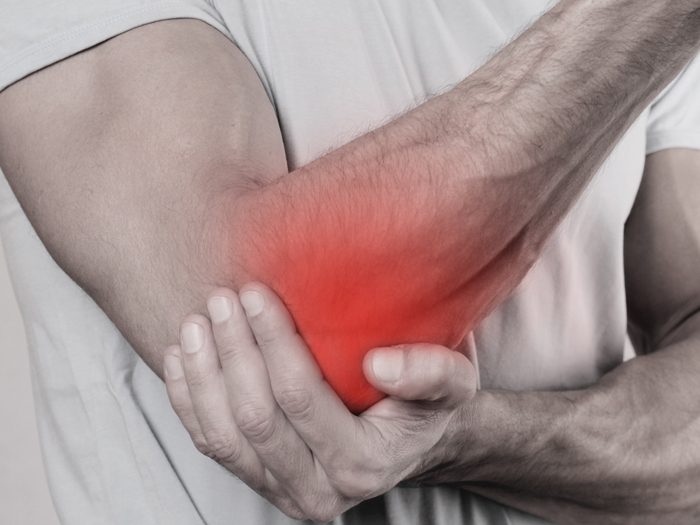
New data has found a connection between musculoskeletal disorders (MSDs) and opioid-related overdose deaths.
The data comes from the Utah Department of Health, the Office of Medical Examiners and the Labor Commission of Utah. In their studies, researchers found that 57% of Utah residents who died from opioid-related overdose deaths had at least one prior workplace MSD.
MSDs are soft tissue injuries that cause pain in the muscles, nerves, tendons, ligaments, joints, cartilage or spinal disks. Most commonly, the shoulders, elbows, hands and lower back are affected. In 2016, the Bone and Joint Initiative put forth evidence that 1 in every 2 American adults has an MSD, costing an estimated $213 billion each year in treatment and lost wages.
This is chilling information for employers who have workers in high exertion occupations that can lead to MSDs, like construction, health care, production, waste management and the like.
But, as one EHS Today article suggests, there is an answer.
The Ergonomic Connection
“MSDs are the result of exposure to biomechanical risk factors such as forceful exertions, awkward postures, sustained exertions, high frequencies and vibration, among others,” said the EHS Today article.
“These injuries occur most often at companies lacking an ergonomics process.”
Ergonomics studies the way people move in their working environment and can play a big role in making sure these workers are doing their tasks in a way that will prevent injury or illness.
When a company is practicing poor ergonomics, “there are social and economic consequences; the most recognizable social consequence is workplace MSDs.”
Properly executed ergonomics, on the other end, can both improve employee well-being as well as enhance business performance. And, with the recent data from the researchers in Utah, proper ergonomics might also curb the still-growing opioid epidemic.
MSDs and Proper Ergonomics
So why aren’t more businesses adopting ergonomic practices?
Well, they have been trying.
In the 1980s, several industries saw the strain MSDs placed not only on their business but also on their workers. A push for better quality ergonomic standards was born. OSHA began tackling the issue in earnest in 1993 but took nearly a decade before it could issue its ergonomic standards.
“It applied to more than six million work sites covering 102 million workers and required all general-industry employers (excluding the agriculture, maritime, and construction sectors) to establish an ergonomics program if triggered by reports of a worker’s MSD or persistent evidence of MSDs in the workplace,” The American Prospect reports.
However, the article further went on to say, “in 2001, Congress rescinded the ergonomics standard that was designed to stem a range of common disabling workplace injuries. Absent regulation, injuries increased and large numbers of people were treated with addictive pain medications.”
But the tide is turning in favor of ergonomics once again, as more and more companies place value into it.
Putting Proper Ergonomics in Place
Ergonomic experts agree that there are several best practices to help implement an ergonomics program that works.
Mark Giordano, a retired ergonomics consultant for the state of Ohio, said it is vital to make sure production leaders (such as engineers, production managers, etc.) are educated and trained on how to identify ergonomic risk factors.
“When designing a process or new product line, they should know what the risk factors could be in their designs and have the opportunity to search for alternatives,” said Giordano in an iReportSource article.
Erica Fichter, SVP of medical management, Broadspire, A Crawford Company, stressed the importance of conducting ergonomic evaluations during the on-boarding process of new employees.
She told Risk & Insurance® that as new employees join the team, trained ergonomic professionals should sit with these workers to review training, movement and use of all equipment and procedures. That way, problem areas can be caught at the start and corrected before injury can even occur.
2017 Risk All Star Joseph Mazza, director of risk management and ADA coordinator for MiraCosta College, believes in the hands-on approach to ergonomics. By becoming an ergonomic evaluator himself, Mazza saved time and created a work environment where employees could come to him right away if they were having a problem at work.
As a result, “we’ve avoided a lot of workers’ comp claims by someone coming up to me and saying, ‘My chair’s uncomfortable,’ or ‘I need you to look at this,’ ” he said.
“Sometimes all it takes is a minor adjustment — or else it’s a major surgery.” &