Metal Manufacturers: Mitigate These Automation Exposures Today
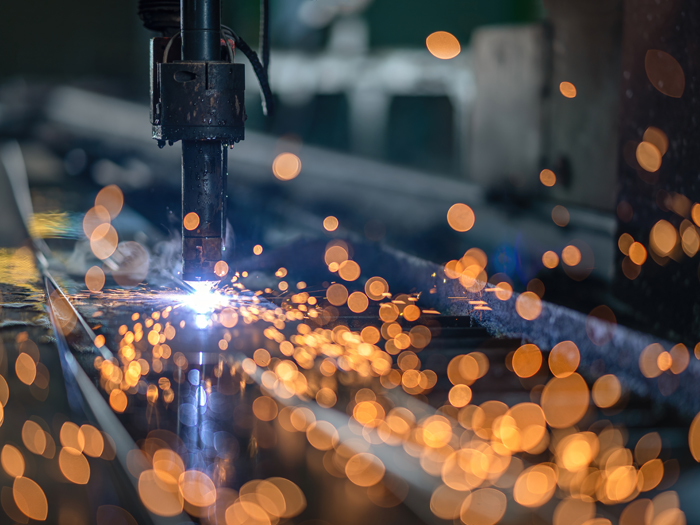
Robotic automation has been a boon for metals manufacturers.
The tools, which can assemble products and reduce repetitive motions amongst workers, are reducing the strain on the industry caused by talent shortages and improving safety.
Robotic technologies prevent workers from completing repetitive motions which, when performed incorrectly, can lead to musculoskeletal injuries.
“These jobs in many cases were ergonomic disasters,” said AJ Steiner, lead loss control consultant with QBE North America.
“Before automation, people were bending, lifting, stooping, and carrying out highly repetitive tasks. Now, that person operates a console instead of doing those risky motions all day every day.”
In 2021, 16% of global metals company executives said their enterprises have invested in robotics for metal manufacturing in 2021, and another 31% said they plan to invest in these tools in the near future, per a KPMG report.
“A lot of these companies are adding automation fast. They’re adding robotics fast,” said Steiner. “What sometimes happens is the safety programs lag behind the changes in the factory floor.”
It’s clear metals manufacturers are eager to implement these new tools. With any new technology, however, comes the potential for new exposures.
Risk managers should consider the effects robotics could have on worker safety, supply chain perils and property risks, so that they can effectively and carefully implement these new tools.
Training Workers to Safely Work with Robotics
Though automating stressful and repetitive motion tasks can improve safety, introducing robotics into a metals manufacturing workplace can increase other safety risks. Catastrophic claims, where someone’s limb or hand gets caught in machinery, can increase with automation.
“We’re seeing more claims involving hands and arms being caught in between machine parts,” said Brandon Hartley, lead underwriter of middle market P&C for QBE North America.
These types of injuries are rare and can be mitigated if employees follow proper safety protocols, but with talent shortages metals manufacturers often face a lot of turnover.
Newer workers might be less familiar with safety procedures. In other cases, manufacturers might turn to temporary staffing firms to fill gaps, and they might not screen workers as extensively.
“To account for that shortage, employers, unfortunately, in some cases are taking maybe less qualified applicants, maybe some applicants who might have past histories worthy of concern or maybe have pre-existing work injuries that raise the risk of being injured on the job again,” Hartley said.
That’s why repeat trainings are key to ensure everyone on the floor understands how to safely interact with robotic tools. Training sessions should target new workers, as well as long-time employees.
Despite their experience, these workers are likely to need instruction on how automation might change common safety procedures.
“You might have a person who welded for 20 years,” Steiner said.
“Well now you’re going to have a welding tech who must oversee robotic equipment that’s doing the welding. That person needs training so they better understand the equipment as well as the hazards.”
Once workers are trained, managers need to ensure they’re following all safety protocols. Floor walks, inspections and other safety checks can all help reduce workplace injuries.
If a supervisor notices something is off, they need to take disciplinary action to ensure the manufacturing facility remains safe.
“I always say with supervisors, your lowest expectation is the highest you can expect from your employees,” Steiner said. “We need supervisors who are accountable and willing to stand up to protect their employees.”
Don’t Forget to Prepare for Equipment Breakdowns and Property Concerns
In addition to safety risks, robotic technologies can shift supply chain and property exposures for metal manufacturers.
On the supply chain end, automation systems often require expensive and unique parts. Some might be sourced from Europe or Asia. If a manufacturer implements these tools, they need to be prepared to repair them in the event of a breakdown — even if the parts are difficult to obtain.
“When we work with a customer, we’re looking at where the material is coming in from, where the equipment is coming in from, how expensive it may be, how easily it can be replaced or if spares are kept on hand?” Hartley said.
Companies should be asking themselves: “If this equipment goes down, how quickly can we get the parts and people necessary to repair it?” Steiner said.
“I’ve heard of horror stories where a company had to wait two weeks because a repair specialist had to fly over from Italy to diagnose the problem, and then they had to have a part shipped in from Italy,” he continued.
Some companies are solving this problem by keeping parts on hand, while others might identify multiple suppliers of a particular part, so they’re covered in the event of a breakdown.
“I know of companies that have $1 million or $2 million worth of critical spares on site because they know their exposure and they want to make sure that they are prepared to replace those parts that might otherwise take six months to acquire,” Hartley said.
Another exposure metals manufacturers might not consider is how automation can increase their fire risk. Though metal isn’t as easily flammable as, say, paper, the plastic crates metal products are often shipped in can pose a risk, especially if stacked on the floor.
Since automation increases the rate at which products are finished, shipping crates might be more likely to be grouped together, creating a fire risk.
“You have to have a specialized sprinkler system to handle that plastic exposure in your storage area,” Hartley said. “If you don’t, you could literally see a building burn to the ground because of the plastics being stored in there.”
Proactive Loss Control Is Key to Implementing Automation
Despite safety, property and supply chain risks, automation still offers metals manufacturers with a number of different advantages. The risks posed by these new technologies are often easy to mitigate, especially when manufacturers take a proactive approach to managing exposures.
One way metals manufacturers can proactively mitigate risks posed by automation is through regular claims reviews with their insurance broker and carrier.
These reviews can help identify injury or loss trends, allowing companies to step in and correct the issue. One manufacturer QBE worked with found that strains and sprains were a common injury, and then implemented a safety training program to target the issue.
“If a claims team member identifies a trend, they work with us and then obviously we’re communicating with underwriting to make sure that we address those specific areas,” Steiner said.
In other cases, loss control specialists can help identify risks before claims occur. QBE’s team looks at historical data and makes risk management recommendations before the insurer offers a quote or binds an account, allowing manufacturers to remain on top of the latest risks.
“We get loss control out there before we quote it, before we bind the account,” Hartley said.
“We’ve already looked at their losses over the last five years with their previous carrier to identify where we can help moving forward,” Steiner added.
This approach allows metals manufactures to improve their risk profiles both by offering reassurance that they understand the risks posed by new technologies and by taking the individual exposures of the business into account. &