Battery Risks
Exploding Exposures
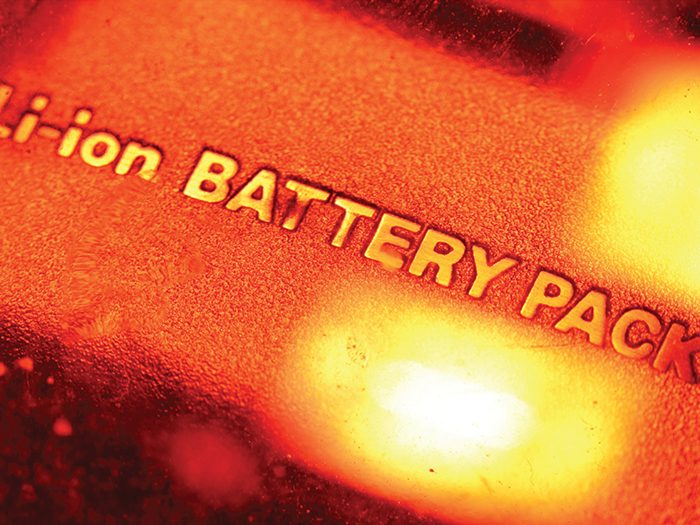
From personal items such as e-cigarettes, cellphones and laptops to power tools, hoverboards, electric vehicles and alternative energy storage, rechargeable lithium-ion batteries (LIBs) come in all shapes and sizes, and are integral to modern living.
But despite their increasing application, the fire risks associated with LIBs have gained publicity of late, piquing the interest of insurers across a range of disciplines, from property and casualty to supply chain to product and environmental liability.
If overheated, LIBs can enter “thermal runaway,” emitting flammable material — sometimes in the form of small explosions; the bigger or more powerful the battery, the more impactful the event.
LIBs include a number of safety features to minimize the risk of thermal runaway. However, overcharging, damage to the battery, using an improper charging device or even excessive discharge can all trigger the problem.
After a UPS plane carrying a bulk LIB cargo caught fire and crashed in 2010, at least 18 airlines, including Cathay Pacific, Emirates and Qatar Airways, banned the bulk haulage of such cargo, causing supply chain headaches for companies transporting LIB products.
There have also been incidents when personal items have ignited in the carry hold on passenger flights.
A study by the Federal Aviation Administration (FAA) showed that gas venting from the batteries had the potential to “rocket” the battery away from the heat source. In a bulk storage facility, this could send batteries off into other parts of the warehouse, spreading the fire.
“If you are selling lithium batteries, it is even more important to have detailed instructions and warnings because there are so many things that can go wrong.” — Paul Owens, products liability manager, Sadler Products Liability Insurance
Indeed, bulk storage situations pose the biggest threat due to the risk of contagious overheating when multiple batteries are in close proximity.
“When you have a lot of these batteries together, fires can grow very quickly and be very damaging,” says Lou Gritzo, vice president of research at FM Global.
However, Gritzo’s firm said it made a major research breakthrough in April that could help mitigate LIB fire risk.
In partnership with the National Fire Protection Agency and the Fire Protection Research Foundation’s Property Insurance Research Group, FM Global conducted a first-of-its-kind warehouse fire test on the type of LIBs used in electric cars and energy storage. The test, he said, identified a sprinkler configuration that provides an “adequate fire protection point.”
Gritzo hopes the test results, which he expects to be published in a few months following data quality assurance checks, can be taken on board as an industry standard.
The results do not resolve the issue of air cargo safety, though some findings may be extrapolated out to develop in-flight fire extinguishing systems and improve safety for LIB cargo transportation.
Beyond the warehouse environment, LIB-powered devices present a product liability risk for manufacturers, importers, distributors and retailers. The biggest hazard lies in importing products that have been installed with defective or even counterfeited batteries that have been repackaged and rebranded to look superior.
In February, for example, U.S. Customs and Border Protection seized 3,500 hoverboards worth $1.8 million that reportedly contained substandard counterfeit batteries that posed a safety risk.
“If you are an electronics manufacturer, it is essential you know who and where you are buying your batteries from, that you are getting high quality batteries, and that they have high thermal runaway thresholds,” said Morgan Kyte, senior vice president and technology team leader at Marsh.
Detailed Warnings Required
The importer of defective goods is considered the manufacturer in the eyes of the law, and in the eyes of insurers in the event of a claim, said Paul Owens, products liability manager at Sadler Products Liability Insurance.
“Importers are top of the pyramid in the U.S. as no one is going overseas to recover,” he said. Most importers are buying from companies whose product liability policies won’t respond in the United States.
“Warning and instruction defect is a common entry into a product liability lawsuit,” Owens added.
“If you are selling lithium batteries, it is even more important to have detailed instructions and warnings because there are so many things that can go wrong.”
“When you have a lot of these batteries together, fires can grow very quickly and be very damaging.” — Lou Gritzo, vice president of research, FM Global
Retailers and wholesalers who purchase from U.S. manufacturers at least know they have a route of recourse in the event of a claim, though it is likely they would be dragged into litigation.
When e-cigarette user Jennifer Reis was set on fire in 2015 when the battery in her device exploded, the e-cigarette’s distributor, wholesaler and even the Tobacco Expo store where she bought it were all named in the lawsuit. Reis was awarded $1.9 million in damages.
“Retailers and distributors should ask their suppliers to name them as additional insureds on their policies,” said Owens.
“If you are named as an additional insured, the importer’s policy is primary and yours is secondary, which is an important step for retailers and wholesalers.”
However, Owen noted, not all insurance carriers are comfortable writing coverage for LIB-powered products.
“You have to be very careful with the policies you buy as some can be very narrowly written — some have full health-hazard exclusions, and for items like e-cigarettes this leaves very little coverage.”
It is not always easy to determine whether a thermal runaway event has been caused by a defective LIB, a defective electronic device or human error, Kyte said.
“Often there is not much material left after one of these, though there are certain tests that can be done and sometimes it is possible to extrapolate a sequence of events to determine the cause.”
Quality Verification
The best way to avoid expensive product liability claims is to only buy and sell LIBs and chargers of the highest quality.
“This will cost you and your customer a little more, but it’s nothing compared to the increase in premiums after a product liability claim,” said Owens.
Lithium manganese (lMR) and hybrid (NiMH) batteries are considered chemically safer than most LIBs and do not require protection circuits, he said.
“Importers need to be good engineers. They should make sure they buy from reputable sources and it is advisable to batch test products that contain LIBs,” he added. &