Ergonomics Is Taking High-Performance Workplaces to the Peak of Safety. Learn How You Can Too
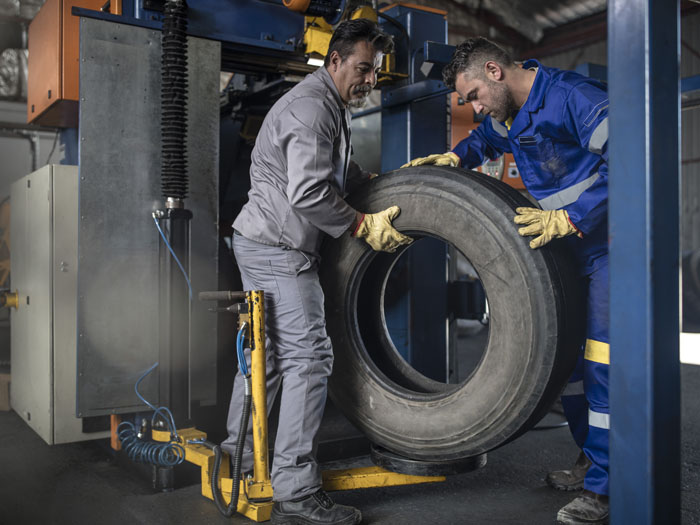
The objective in ergonomics is prevention medicine, said Matt Jeffs, doctor of physical therapy, safety management professor and ergonomic specialist educator and principal faculty, The Back School.
As a 30-year veteran and expert in keeping workers safe and improving ergonomic standards, Jeffs knows a thing or two about what it takes to have effective ergonomics within a company’s safety program. After putting in 12,000 hours at a paper mill in North Florida, Jeffs was able to develop a system that aimed to help these high-performance workers achieve top safety through lean continuous improvement.
On April 20, as part of the National Ergonomics Conference’s continued efforts to bring attendees top ergonomics news and reports throughout the year, Jeffs will talk more in-depth on this very topics.
Jeffs’ session, “Physical Demand Gap Analysis – The Bridge Between High-Performance Workforce and Peak-Safety Workplace,” will ease attendees into this world of ergonomic evaluation by discussing the Five Why Root Cause Analysis questions.
“We use that phrase, ‘five why,’ but what that really means is asking why did an event happen. Then, you just keep asking why until you can’t answer it anymore. Sometimes that could be three whys and sometimes nine, depending,” he explained.
The goal of the five whys is to get to the root cause of an issue. Once determined, the team can begin to figure out ways to address and prevent future injuries before they arise.
The Physical Demand Analysis and Lean Continuous Improvement
In the early 1990s, Title I of the ADA gave ergonomists permission to examine job title essential functions, so that they could better bridge the gaps between the workforce and their work tasks.
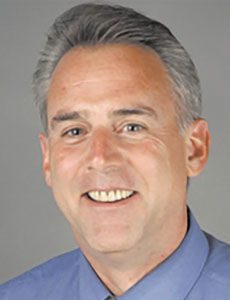
Matt Jeffs, doctor of physical therapy, safety management professor, ergonomic specialist educator and principal faculty, The Back School
But, according to Jeffs, execution on the law’s intent fell short.
“There have been examples in the ensuing years where some outfits really didn’t honor the spirit of that law,” Jeffs said. “But this law was designed to actually help people work safer and more secure. That’s what we’re doing now with physical demand gap analysis.”
Physical demand analysis, or PDA, sees ergonomists and others devoted to improving safety on the job gathering job-specific data to help improve operations. That means looking at how often a person sits, lifts, carries, pulls, kneels and more while on the job.
“We ask workers pointed questions about their work, especially what they find most fatiguing,” said Jeffs. “Then we follow them into the field or out onto the operations floor to observe some of the things they highlighted in that initial 15 to 20 minute interview.”
That information is then measured through repetition.
Jeffs likened it to CrossFit: “We set up into a six station cycle that the worker goes through” in which they repeat the motions discussed and reviewed during their evaluation. “We’re not looking for speed. We’re looking for certain performance metrics. Do they counterbalance a lot, do they recruit more muscle than necessary? That’s all designed to see the demands of the job and to develop strategies to close the gap.”
Through streamlined PDA screening, Jeffs said workplaces can eliminate exposures when 1) onboarding new talent, 2) evaluating incumbent talent and 3) recovering return-to-work talent.
“This tool is designed to improve the performance of the workforce, while at the same time reducing the risk of the workplace,” he said.
Attendees will come away from the April 20 session with a deeper knowledge and understanding of the real application of PDA as it pertains to lean continuous improvement. To learn more or to register for the session in advance, visit the ErgoExpo registration page here. The session will be held at 2 p.m. and will be available for digital download after the event. &
National Ergonomics Conference and ErgoExpo is back and planning an exciting program for 2021. We’re eager to bring everyone together to share the tools and ideas that will move our community forward through the challenging times ahead.
We’re eager to get face-to-face with our friends and peers again — safely in our Vegas home at the Paris Hotel, November, 2-5, 2021. We’re currently building an exciting program for the show and look forward to seeing everyone in-person while still adhering to all safety protocols set forth by local and national health authorities at the time of the event.
The National Ergonomics Conference is proud to continue to offer thought-provoking ideas and tangible tools and strategies to help ergonomic and safety professionals improve productivity, product quality and profitability while reducing workplace injuries. This year, we’ll feature five tracks — program management, office ergonomics, advances in ergonomics technologies, industrial ergonomics and safety, and health care ergonomics, aging and wellness.
In the meantime, we’ll continue bringing you free virtual, educational content through our digital sessions series. Register today so that you never miss a session and check out our ever-growing library of on-demand sessions today!