Regulatory Watch
A Salary Threshold Working Over Time
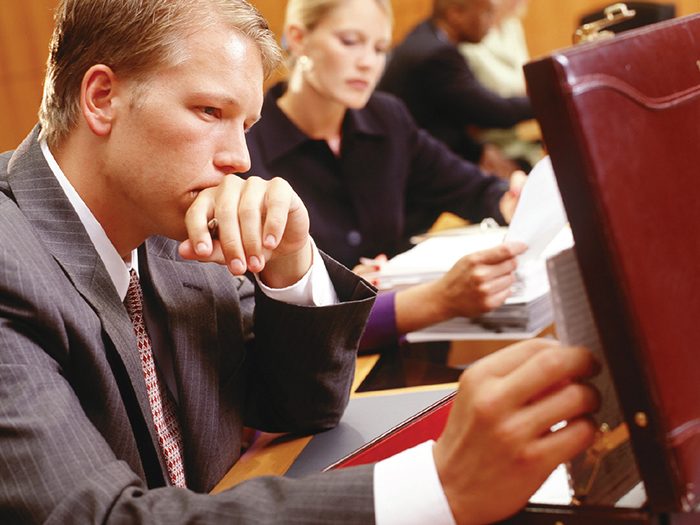
New U.S. Department of Labor rules may require employers to pay overtime to salaried workers earning less than $47,476 a year, effectively doubling the current overtime annual salary threshold of $23,660.
A group of 21 states and more than 50 business groups that filed suit against the DOL won a preliminary injunction in late November that halted the rule from taking effect on Dec. 1. The election of Donald Trump to the presidency and his promise to roll back regulations add more uncertainty as to whether this new rule will be revoked or revised in 2017.
The Department of Labor estimates as many as 4.2 million U.S. workers would be affected by the change. By some estimates, as many as 70 percent of companies are in violation of the rules.
It’s important to conduct an audit of your workforce and bring all employees to compliance if they are not already, said Catherine K. Ruckelshaus, general counsel at the National Employment Law Project.
With many existing state rules already much higher than the federal threshold, companies often find they are already in compliance, which is much more cost-effective than defending a wage and hour claim.
But with so many companies still at risk of being noncompliant, they must review for problems, said Chris Williams, an employment practices liability product manager at Travelers.
“If you haven’t fixed it … [and you are sued], you paint yourself in an even worse light in a courtroom,” said Lisa Doherty, co-founder and CEO of Business Risk Partners, a specialty insurance underwriter and program administrator.
Wal-Mart Stores was most likely aiming for broad-based compliance ahead of the deadline when it recently raised all salaries for its entry-level managers to just above the threshold at $48,500 from $45,000 annually, according to Reuters.
A Change Long Overdue
The FLSA was enacted in 1938 and established the 40-hour work week salary threshold, which entitled workers to time-and-a-half their regular hourly wage for any overtime.
White collar workers making more than the threshold and meeting certain “duties tests” were exempt from receiving overtime pay if they worked more than 40 hours in a week. The current threshold of $455 a week or $23,660 annually, has been in place since 2004.
“A mid-level manager with a labor budget and no compliance training regarding overtime rules is a loaded weapon you have pointed at the business because you have given that manager an incentive with no context.” — Noel P. Tripp, principal, Jackson Lewis P.C.
The currently postponed new rule more than doubles the minimum to $913 per week, or $47,476 annually, and will automatically increase every three years based on wage growth Employers with exempt salaried workers within this range generally face three options.
One: Raise the annual pay to above $47,476 to maintain the exempt status. This option works best for employees paid a salary close to the new level, such as those Wal-Mart managers.
Two: Reclassify salaried employees as hourly and pay time and a half when they exceed 40 hours in a week. This approach works best when there are only occasional spikes that require overtime for which employers can plan for and budget.
Three: Strictly limit employees’ time to 40 hours and hire additional workers. That’s not always a welcome path if it triggers a new record-keeping system to track hours. It can be difficult to get workers to change their behavior to start recording when they arrive at work and leave.
Establishing a 40-hour week was meant to encourage employers to hire more people rather than pay overtime, but often adding staff is not in the labor budget.
“A mid-level manager with a labor budget and no compliance training regarding overtime rules is a loaded weapon you have pointed at the business because you have given that manager an incentive with no context,” said Noel P. Tripp, a principal at Jackson Lewis P.C., who represents employers in wage and hour cases.
What’s at Stake? Legal Cases Are Growing
There were 8,000 FSLA wage and hour claims filed last year, making it the single fastest growing type of employment litigation, Doherty said.
One reason for that claims volume is that there are a variety of ways a company can violate the rules.
There’s straight-out failure to pay overtime when a worker is entitled to it. There’s “donning and doffing” claims when an employer doesn’t include the time to put on protective gear as part of the work day. DuPont and Tyson were both targets of class action lawsuits citing donning and doffing.
“It has been the law for many decades; if you don’t keep track of it there’s a presumption against you,” said attorney Thomas More Marrone, who is representing employees against DuPont.
Some newly emerging FLSA cases involve the time employees spend on computers or checking email at home, Williams said. Often, he said, it’s not until a claim is filed that employers — who bear the burden of proof in most cases — realize they haven’t maintained the appropriate records to defend the business.
It’s important that companies talk to a broker about coverage for some of that exposure, Williams said.
A coverage endorsement attached to employment practices liability insurance (EPLI) policy forms may cover the cost of defending claims alleging that an employer failed to pay overtime to a nonexempt employee. &