Three Powerful Technologies Are Joining Forces to Revolutionize Workplace Safety
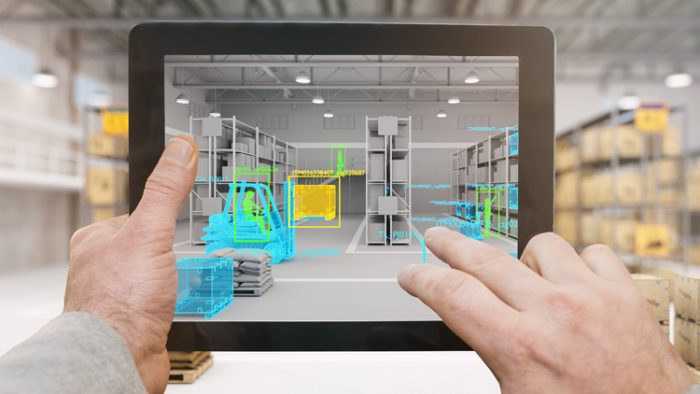
Ask people in 2019 what a “virtual worker” is, and most might suggest an employee who works remotely in the gig economy. Or, perhaps, they might say some form of artificial intelligence automating a manual job. But soon “virtual worker” may mean something entirely different.
In the coming years, sensor-laden wearable technology (wearables), virtual reality (VR) and augmented reality (AR) are set to converge, revolutionizing workplace risk management. These technologies are slated to allow employers to use virtual workers as a way to review the physiological limits of a task before sending a live human to do it.
Wearables already transformed our understanding of the impact of work on the human body. Real world data is gradually being aggregated to help employers manage staff more safely and efficiently. Soon there will be enough to confidently simulate human physiology and work environments.
Real workers could also be employed to simulate body movements in simulated environments — think Andy Serkis strapped to electrodes to create Gollum in the Lord of the Rings franchise — adding volumetric body reconstructions to the dataset.
“2020 is less than two years away, by which time 40 percent of the workforce will be millennials who will expect this kind of training.” — Kate Barnes, underwriters counsel, Swiss Re Corporate Solutions
“We think AR and VR is the next frontier when it comes to workplace health and safety,” said Lars Skari, managing partner of Altumai, a tech firm dedicated to advancing the application of wearables in the workplace. “There is a lot of disparate technology and data begging to be integrated.”
Altumai’s “connected worker platform” aggregates data from various wearable sensors and other data sources, including smart phones — which Skari believes will complement or supplant wearables in some use cases — then feeds that data back to clients in the form of risk mitigation advice.
Most of this work has so far been in agriculture: “Agriculture presents a unique set of connectivity and environmental challenges,” said Skari. “We felt that if we master that, everything else will be relatively straightforward.”
The Wearable Revolution
Wearable tech has advanced significantly in just a few years. Its origins were in tracking single movements, such as bending at the waist, but its scope quickly widened — not always with success; the AIG-backed startup Human Condition Safety, for example, filed for bankruptcy as recently as January.
Nevertheless, the sector has more success stories than failures. Ford’s SafeCap is a well-known example, monitoring truck drivers’ brainwaves to detect tiredness, instructing them to pull over and communicating with headquarters.
Real-time worker location systems are now commonly employed in hazardous environments such as building sites to ensure people don’t walk into no-go zones and to track people quickly in the event of an accident. Once employers know what activities are driving injuries and accidents, they can better allocate resources towards safety and procedural training.
And it is little surprise more companies are taking this concept seriously. U.S. businesses spend around $60 billion annually in workers’ compensation premium, and in labor-intensive industries, this spend can be the largest single ongoing expense.
“A lot of time, money and technology are being applied to the connected worker space. Network, sensor and IoT capabilities have steadily improved and can now give us meaningful data. We are suddenly at an inflection point, and companies are now starting to realize the value,” said Doug Turk, chief marketing officer, JLT Specialty USA.
He cites Altumai’s platform, Modjoul, StrongArm and Triax among the companies whose platforms are turning wearable data from useful information to actionable data.
According to Skari, its systems have the capability to cut musculoskeletal injuries by a third and the potential to significantly reduce claim severity, frequency and processing time. “If you can reduce worker absenteeism and improve the work environment so that workers are more effective, productivity goes up and so do revenues,” he added.
With the dataset on worker behavior growing all the time, simulated models of work environments and behaviors are inevitable — and this is where VR and AR technology comes in.
Converging Tools
Today, virtual reality is used primarily as a training tool. Employees don a VR headset and can instantly practice flying an airplane, handling hazardous materials or operating a forklift truck without putting themselves or others in danger.
“2020 is less than two years away, by which time 40 percent of the workforce will be millennials who will expect this kind of training,” said Kate Barnes, underwriters counsel for Swiss Re Corporate Solutions.
She is already seeing strong uptake of VR in the construction sector, where trainees can navigate increasingly large, complex and hazardous projects through simulations. And Barnes thinks the integration of VR, AR and wearables is a natural fit: “We tell our clients the future is now,” she said.
Indeed, it is not a huge leap to see how VR simulations can be integrated with data gathered from wearables or other IoT, such as proximity or environmental sensors, then supplemented with AR to create a powerful risk management matrix.
“Wearables are just one piece of the puzzle,” added Turk. “Once you have that data, you can then employ VR and AR to create a virtual worker model to show how certain roles should be conducted.”
Simulated workers can be stress-tested against certain industry-specific variables, such as temperature or yield in a strawberry picking field, for example. The next iteration would be to overlay AR onto real world environments to assist safety officers with risk mitigation and training.
Floor supervisors could, for example, overlay a camera or lens over the work environment in question. Their screen will show how each workers’ movements compare to ideal ranges of movement. It could also detect an employee’s propensity to get injured, as well as offer training cues.
“Wearables and IoT will give rise to more data, which will allow AR and VR to provide a richer experience. The ability to interact with the physical data in this more visual way makes it much more actionable, allowing us to coach and provide directional guidance more effectively,” said Skari.
This is all leading to a future in which each worker has a real-time risk score that is constantly monitored. The impact on insurance premiums could be significant for companies and can provide robust data demonstrating how work behaviors and incident rates have improved.
“Any safety improvement has to be considered in pricing,” said Barnes. Alternatively, Turk thinks access to these insights could encourage more firms to choose adaptive self-insurance for workers’ comp.
Making the Leap
But when will this become a reality? Skari believes the way we interact with data will change dramatically in the next two to three years thanks to the rise of 5G and further improvements to 3D modelling techniques.
“Will it change dramatically within the next year? Perhaps not,” he added, though he revealed his company is working on a smartphone app that would allow the user to scan the work environment and to see risks and mitigating coaching factors pop up on the screen for each worker.
“We’re closer than we think,” said Turk. “If we consider the human body as a machine, once we have enough data to understand how the machine operates, we can quite easily conduct virtual stress tests,” though, Turk added, he doesn’t expect to see this kind of system in use for a number of years.
“Network, sensor and IoT capabilities have steadily improved and can now give us meaningful data. We are suddenly at an inflection point, and companies are now starting to realize the value.” — Doug Turk, chief marketing officer, JLT Specialty USA
The primary challenge is to build a large and reliable dataset from which to model workers and work environments. Data processing power is of course a key hurdle — wearables generate enough data on their own without the computational demands of VR or AR also being thrust upon a single server.
Then there are ongoing issues around the consent of workers and the privacy and security of data generated by wearables. However, these challenges are surmountable, and virtual worker simulations are an inevitable next step. Those companies that partner with insurtech experts to develop models of their own workplaces may just unearth a game-changing influence on their bottom lines. &