Behavior-Based Safety
Taking a Bottom-Up Approach to Safety
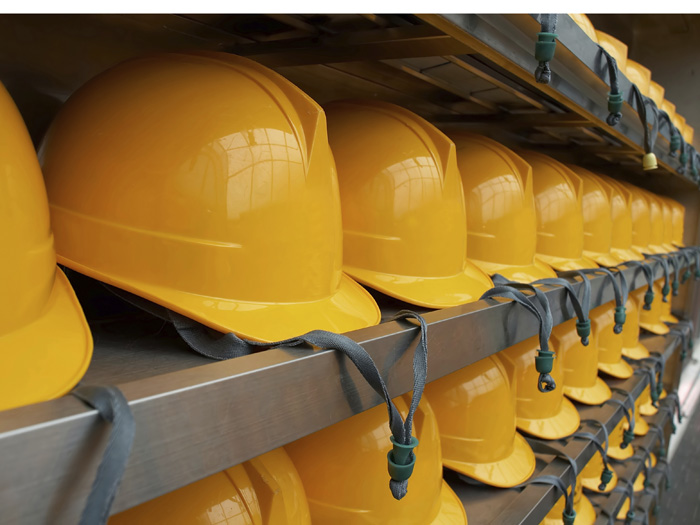
The best way to cut workers’ comp costs is to eliminate claims. The most effective way to prevent claims is to reduce workplace risks.
Behavior-based safety (BBS), a bottom-up approach that stresses positive reinforcement of safe behavior in the workplace, is one method that has been used with varying degrees of success. An Illinois-based manufacturing company is looking to behavior-based safety to ramp up its safety culture, and it hopes to eliminate risks to employees.
Identifying Champions
BBS is essentially the process of applying the science of behavior analysis to workplace safety issues. Or, as Texas Mutual explains, it is “a process that helps employees identify and choose a safe behavior over an unsafe one.”
BBS requires the participation and engagement of all employees from executives to hourly workers. Unlike other safety programs, BBS relies heavily on buy-in from nonmanagerial workers.
“One important aspect of this program needs to focus on whoever the ‘champions’ are that they be hourly people,” said Julia Sfurm, corporate risk operations manager for Illinois-based Elkay Manufacturing. “It needs to be someone considered one of them, as among their peers, instead of being a manager or a supervisor. That becomes a different role than having one of their own contemporaries give them feedback.”
The champions are a vital part of the BBS process, according to Sfurm, who, has worked with her team and others in assisting with the coordinated rollout of a BBS observational program in the organization.
“The idea is to engage employees in a safe culture,” she said. “You want them to work in an environment where safety is important, to be aware of their surroundings, and try to reduce or eliminate potential risks or [workers’ comp] claims.”
The program involves setting up teams of employees, each with one or two champions who lead the groups and help determine how best to move forward to change unsafe behaviors. An individual or group of employees observe one another performing routine work tasks to see whether specified safe behaviors are being followed.
The safe behaviors are typically listed on a checklist form, consisting of no more than 10 items (see box). The observers then provide feedback to the employee who was observed.
Positive vs. Negative
Positive reinforcement from a fellow worker is vital to the success of BBS. “It should not be used as a tool or punishment because you would lose effectiveness,” Sfurm said. “That’s not the purpose.”
In fact, blaming is among the top reasons some BBS programs are met with resistance from workers, especially unions.
“Believing, teaching, or assuming that most accidents are caused by unsafe behaviors of workers. Starting with this flawed premise creates a shaky foundation and instant animosity for a behavioral approach,” wrote Terry L. Mathis, the founder and CEO of ProAct Safety, a company that provides safety excellence strategies. In an article Unions and Behavior Based Safety: The 7 Deadly Sins, Mathis says “ignoring conditional and organizational issues that can cause both accidents and unsafe behaviors is a formula for failure: failure to produce maximum results and failure to solicit union support.”
BBS works best when workers are treated with respect and feedback provided on their safety habits is given in a non-threatening way, Sfurm explains.
“For every one negative you tell them, you should tell them three or four positives,” Sfurm said. “You don’t want to create an environment where every time they see a [particular] person coming near them they say, ‘oh boy, I am being watched.’ That changes behavior. You want a relaxed and normal working atmosphere.”
For example, someone driving a forklift might be observed to see if he is using a horn when rounding a corner, wearing a seat belt, and driving at a safe speed.
The observer would later “go up to that person and say, ‘I saw you driving a forklift, and you were wearing a seat belt and blowing the horn and that is really good,’ and then that’s where you say, ‘but you’re driving like Mario Andretti,'” Sfurm said. “Or instead you could say, ‘I see you were doing these two activities well, is there anything you think you were not doing well?’ That gives them the opportunity to say, ‘I was going too fast.'”
Changing Behavior
Observers are asked to fill in the checklist forms throughout the day and place them in a box or area that is specifically for the champions, who should review them daily. Doing so can flag problems that need to be addressed.
“You may find out why a certain behavior is going on,” Sfurm said. “For example, is the person observed as being rushed? This is where an assessment of the process can be undertaken to determine if it is an individual issue, are products coming too fast, or is there a problem with a product and something needs to be fixed. If [the champions] see multiple forms for the same activity (everybody is speeding), you could go to the person in charge of the plant or activity and say, ‘based on some behaviors, I believe all drivers need to be retrained.’ In this way, as a champion you are identifying a corrective action to the behavior but no one is getting anyone in trouble. It’s a way to say ‘I see an unsafe behavior and I need to correct that.’ It’s more of a positive reinforcement than a negative reinforcement.”