Food Safety
How the IoT Is Making Food Supplies Safer
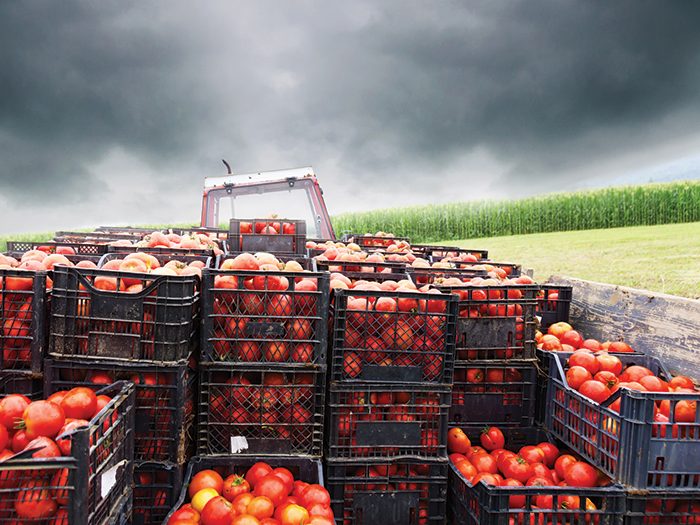
The Internet of Things is improving transparency within the food supply chain — from farm production, to monitoring processing and shipping, to determining food quality on grocery store shelves and even in home refrigerators.
“IoT is becoming increasingly important, especially within the food supply chain, as consumers want to learn more from farm to fork,” said Shaun Kirby, a director at Cisco Consulting Services in San Jose.
“IoT helps companies collect and track information to address issues in a timely manner, such as problems that could cause foodborne illnesses.”
Cisco, in conjunction with Penelope S.p.A. and NTT DATA, helped the Barilla Group implement a platform called Safety for Food, enabling consumers to trace the production chain for the ingredients in their food. Powered by ValueGo® software, consumers scan a QR code on the back of products to access a website that tells the story of the specific batch of the product they bought — from where the ingredients were grown to how the product arrived on the store shelf.
More companies are using “fog computing” in the field to analyze data from IoT devices faster, Kirby said. For example, a sensor on a truck could catch a dip in temperature, transmit the information to the cloud and take local action to correct the situation, he said.
“Fog computing enables companies to make more intelligent decisions at the edge, where devices are very low cost and constrained, or the actions can be coordinated at higher levels on [the] cloud.”
Other devices include ethylene gas sensors that detect produce spoilage on trucks, in warehouses or on grocery shelves, and hyperspectral cameras that detect light reflected from foods to determine whether they’ve gone off, Kirby said.
“These applications could one day be used throughout the supply chain, but right now, they are large and expensive to install, so they’re better suited for large centralized facilities,” he said. “As the sensors become more commoditized, they will become smaller and less expensive, so they can be used downstream within the supply chain.”
Cisco’s experts are watching the development of a new infrared spectrometer for consumer use. It’s a pocket-sized device that conducts chemical spectrum analysis on almost any product, Kirby said.
A significant challenge is managing data collected from all of these devices. Today, there are about 200 devices per information technology worker to manage, but as the use of IoT increases that number could jump to 1 million devices.
Sean Riley, global industry director of manufacturing and transportation at Reston, Va.-based Software AG, said companies can utilize sensor data related to the food products to ensure optimal quality.
“Spoilage … is not necessarily noticed in advance, especially when it is a product that is going to be utilized in the processing of a finished food,” said Riley, who works from Chicago.
“Testing can be used to determine the state of the product at that time and then be used to draw inferences to the life left of that product, but it requires time and resources.”
Data from IoT devices throughout the food supply chain can be coordinated to ensure products are handled appropriately with regard to temperature, light and other environmental metrics, he said.
“As IoT evolves, I envision it will help us proactively prevent foodborne contamination from happening altogether.” — Richard Bladek, national underwriting manager of food and beverage, Starr Companies
“For example, bananas spend a significant amount of time ripening and the amount of airborne chemical used to ripen them is selected at the beginning of the journey,” Riley said.
“An IoT sensor can provide information regarding the ripening process and may be used to trigger an event to inject more or less chemical into the environment to shorten or lengthen the ripening process. This would, of course, be based on the in-transit time to the final destination and the need at the final destination.”
Previously, growers provided discounts to push ripened product, but the use of IoT devices now enables them to gain a greater amount of control over the ripening, in turn giving them more time to locate suitable demand, he said.
“This information could also be made available to consumers, so they can understand where their products have originated from with certainty.”
Using IoT within the food supply chain can help insurance companies better track the sources of food when a claim arises, said Richard Bladek, national underwriting manager of food and beverage at Starr Cos. in Chicago.
The use of IoT would help identify the food manufacturer and processor, especially if there are multiple manufacturers and processors used for a single product.
IOT in Underwriting
From an underwriting perspective, IoT helps carriers determine whether clients have safe processes in place, and enables them to address potential issues early, Bladek said.
IoT can also help track contaminated items before they get into a food product and are passed on to the general public.
“As IoT evolves, I envision it will help us proactively prevent foodborne contamination from happening altogether,” he said.
“As underwriters, we’re analyzing data constantly. We could use this information to help insureds manage their business through loss control. … The data derived from [IoT] could enhance our capabilities internally to help our insured prevent losses from occurring in the future.”
Some farms are using IoT sensors to track climate and weather to improve crop yields, said Leslie T. Krasny, a partner in the San Francisco office of Keller and Heckman LLP.
The use of radio frequency identification can locate food in transit and reroute shipments for efficiency, such as when there are hurricanes, snowstorms or landslides, she said. This can allow for the purchase of replacements to meet customer commitments.
There are cameras with software that can help detect foreign materials in foods during processing, and significant variations from specifications, which could prevent adverse health effects, damage to corporate reputation, and product loss.
IoT is a tool with great potential for food supply chains, but it will make the liability equation within the supply chain more complex, said Christopher G. Van Gundy, another Keller and Heckman partner.
If food transported in a refrigerated truck with automated temperature control arrives spoiled at its destination, the device manufacturer could be an additional source of liability, Van Gundy said. Questions could arise about whether the device was set and functioned correctly, and who bore responsibility for that task.
IoT devices in the supply chain also can increase regulatory compliance liability, he said.
“Regulators like the FDA might start requiring that companies show them their data to determine if they are in compliance with food safety regulations, such as tracking data for pathogens,” Van Gundy said.
“This could create a dilemma for companies that want [enough data] to monitor their pathogen situation, but don’t want to draw the attention of [the] FDA to potential problems that may not exist.” &