Teddy Award Finalist
Energized Safety Performance
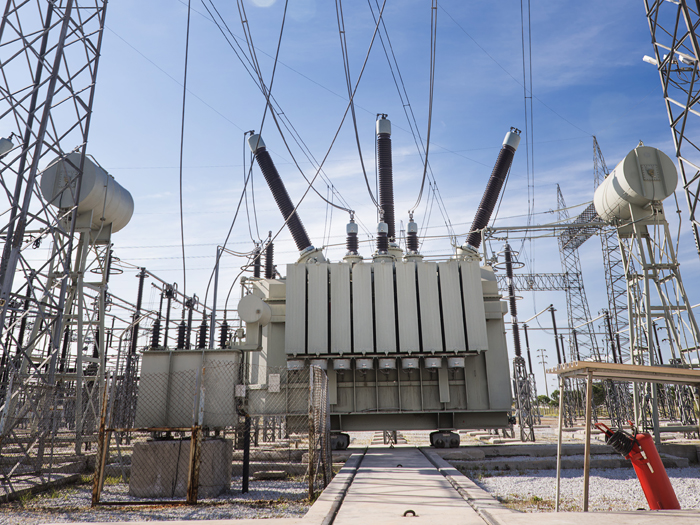
No technological advance in America in the past 150 years quite matches, in its effects on society, the impact of electrical power and light. Since its origins in the late 19th century, Phoenix-based Pinnacle West Capital Corp., has delivered this advance to one of the two-fastest growing states in the nation.
And it has performed this essential task with an ever-improving focus on safety. The organization’s focus on personal and industrial safety has contributed to a significant reduction in injuries in the last five consecutive years, resulting in a 57 percent drop in OSHA recordable injuries since 2008. The company’s safety record is about twice as good as the electrical utility industry’s average in frequency and severity of injury.
The company’s electrical power linemen work under extremely high risk. They represent the tip of the iceberg of injury risks, large and small, that a modern power generation and distribution workforce of 6,600 faces.
Its largest affiliate, Arizona Public Service (APS) serves more than a million customers in 11 of Arizona’s 15 counties and is the operator and co-owner of the Palo Verde Nuclear Generating Station, a primary source of electricity for the Southwest. APS is the second fastest growing electric utility in the United States over the last five years and is also a leader in the development of solar technology.
Approximately 70 percent of Pinnacle West’s employees work in highly specialized craft, operations, technical, engineering and customer-service positions. These positions have job-specific training requirements that range from 16 to 400 hours annually.
The closer one looks at the company’s work safety practices, the more an engineering-type culture of attentiveness and problem-solving emerges as a major driver.
Tools have been introduced throughout the company to further improve safety performance, which is measured daily using Event Free Clocks. The Event Free Clocks are used to help recognize errors, learn from mistakes and prevent similar events from occurring.
These clocks are placed prominently around operational work environments and office locations to give employees an ongoing visual reminder of safety performance.
The company also created a Corrective Action Program (CAP), designed to drive continuous improvement by identifying, tracking and resolving unfavorable conditions. It uses self-assessments, common cause analysis and audits
The biggest workers’ compensation challenge that Pinnacle West has focused on during the past five years is mitigating the consequences of highly demanding and physical work on an aging workforce. For example, linemen must operate heavy equipment, climb poles and perform overhead work, often in awkward and strenuous positions. And many employees work out of doors.
The physical demands of the work cannot be eliminated due to the very nature of producing and delivering power through a massive infrastructure of power plants, transmission lines and distribution systems. The strenuous nature of the work becomes even more challenging with an aging workforce.
Pinnacle West controls its medical costs and ensures quality care for its workers by self-insuring its workers’ compensation and integrating it with absence management and return-to-work programs. It has developed a comprehensive program of health and wellness programs.
The company’s workers perform essential services for Arizonans in a work environment dedicated to safety and health.