Sponsored: AXA XL
These 5 Technologies Are Solving Construction’s Safety and Productivity Problems
More than nine-hundred people die every year in construction worksite accidents in North America — just shy of three people each day. At the same time, labor-productivity growth for the industry averaged just 1 percent for the past decade, compared to 2.8 percent for the total economy.
Underlying both of these problems could be a lack of innovation. For the most part, people still build the same way they did 100 years ago.
New technologies, however, are beginning to take their place on the job site and show real promise to boost safety, productivity, project quality and recordkeeping capability.
“The upside to new construction technologies is almost limitless,” said Gary Kaplan, President of North America Construction, AXA XL. “Like any industry, construction companies need ways to capture more data, analyze that data in real time and turn it into actionable insights. Doing so can make a positive impact on nearly every aspect of the construction business.”
Though new innovations emerge every day, these five technologies are effecting change in construction today:
1) Wearables
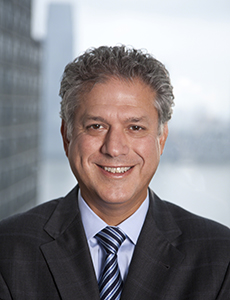
Gary Kaplan, President of North America Construction, AXA XL
Wearable wristbands, hard hats, belts clips and vests are unlocking the possibility of detecting and eliminating unsafe behaviors before they result in an injury.
“These digital devices collect the data that enable project managers and supervisors to be proactive in correcting unsafe conditions,” Kaplan said. Personal wearables detect movement like falls from height, recording the length and speed of the fall. While this information can be used post-incident in claims adjudication, it can also alert managers to dangerous activity before an injury happens.
“There was a scenario once where a wearable was detecting one worker falling at the same time every day. It turned out he was sliding down a bannister on his way to lunch. Once that behavior was known, it could be stopped, which eliminates some potential for harm,” Kaplan said. “You see the same thing with workers jumping off the back of trucks. It seems innocuous, but it’s an easy way to get hurt.
More advanced personal wearables measure heart rate, body temperature, perspiration and other biometric data that can prove critical in preventing everything from fatigue to heat stroke.
The location-tracking capabilities of personal wearables, along with equipment trackers and BIM technology, can also help contractors improve productivity by better planning work sequences and more efficiently utilize the layout of site to reduce downtime.
“Wearables can tell you how many steps or how long it took a worker to go from point A to point B,” Kaplan said. “That allows project managers to reconfigure things like where materials are laid down, and where the restrooms and break areas are located.”
2) Equipment Tags
Equipment-mounted sensors similarly improve both productivity and safety by allowing for real time tracking of location and utilization. A record of a machine’s idle time versus active time provides contractors two key insights: high idle time indicates the machine could be put to better use elsewhere, while high usage could indicate the equipment may be due for maintenance.
“Proactive machinery maintenance reduces downtime. Sensors let operators know exactly when a key piece of equipment could use a tune-up,” Kaplan said. Tracking the location of equipment means it can be moved into place before a work sequence is scheduled to begin, minimizing delays.
When used in combination with workers’ wearable sensors, equipment sensors also help to keep unqualified employees away from the controls of dangerous machines. If an employee is too close to a piece of equipment for which they do have authorization to operate, the wearable sensor sends an alert to a centralized dashboard, which also maintains a database of all workers’ certifications and clearances.
“The supervisor on site can intervene and make sure the unqualified worker doesn’t take control of that machinery,” Kaplan said.
3) Atmospheric Sensors
Site sensors that detect environmental conditions on the job site have benefits for worker safety and quality assurance.
“If you have high humidity or lots of particulate matter in the air when you are doing work, for example, it could compromise its integrity,” Kaplan said. Sensors can also be placed in between interior and exterior walls to detect moisture that could lead to mold. Failing to catch and remediate the issue early could result in construction defect claims down the road if the mold spreads.
Atmospheric conditions also include things like noise, which could distract workers and prevent them from hearing vital instructions, and wind, which increases the risk of falling equipment. Sensors mounted throughout work zone can emit alarms or send alerts directly to wearables to increase workers’ awareness. They can also be designed to detect smoke and heat to detect fires.
Historical atmospheric data also adds another dimension to project records beyond typical information like schedules and inspection reports.
“If issues arise in the future, environmental data gives stakeholders a better idea of what exactly was going on at the time the work was completed,” Kaplan said.
4) Building Information Modeling
BIM models create digital representations of both the physical and functional characteristics of a building. Advanced versions also incorporate time and cost, providing a complete picture of project scope. More importantly, they are shareable among all a project’s stakeholders, so architects, designers, and contractors can all contribute data.
“BIM models allows you to see how everything interacts together as different phases of the project are completed,” Kaplan said. “When incorporated into the pre-planning phase, BIM enables more efficient scheduling of work sequences. This means you don’t have to go back and fix things that were done out of order, and you don’t have people standing around waiting for their turn.”
BIM technology also yields new benefits for quality assurance when connected to advanced imaging tools. Real time images can be compared to BIM models to ensure work is completed to the prescribed standard.
5) 3D Imaging and Digitized Inspection
Digitizing the inspection process also goes a long way in detecting defective work early. “New imaging technologies let you take high-definition 360-degree images of the project at different stages. You can then compare those to the BIM model to make sure everything matches up. It’s a much more effective way to catch mistakes compared to visual inspections,” Kaplan said.
Digital records offer a huge advantage over paper-based recordkeeping. Given that construction defect claims often are not filed until multiple years after a project is completed, building a defense requires hoping every stakeholder has held on to those paper files and kept them in good shape.
All of these technologies together – wearables, equipment and environmental sensors, BIM models and imaging — create extremely detailed records so owners know what work was done, by which party and when.
“Having a permanent record makes liability for a defect much more clear, which can shorten the length and drastically reduce the cost of a defect claim,” Kaplan said. “Even if a claim is never filed, good documentation is just good practice. Large projects are complex, and having a record of work helps keep it in order.”
Underwriting to Enable Construction Innovation
Kaplan applies construction’s project-centric management style to his own team at AXA XL, using it to drive innovation.
“We use projects to drive innovation. We challenge our team to identify ways we can improve our operations, our products, our customer service, or the risk selection of our clients. Then we launch a pilot to test the solution,” Kaplan.
The team executes more than 50 projects per year. One of the more recent experiments involved partnering with a weather analytics company and using its data to “engineer the weather risk out of construction,” Kaplan said. “Planning ahead for weather patterns helps avoid a lot of the damage that results from a potential storm.”
The expertise developed through these projects will enable the AXA XL construction team to become third-party validators of new, innovative technologies entering the industry.
“We hope to be more like consultants in the Insurtech space,” Kaplan said. “Especially now with the combined resources and expertise of AXA and XL, we can be more responsive to the fast pace of technological change and the needs of our customers.”
To learn more, visit https://axaxl.com/insurance/industry-insurance/construction-design-insurance/contractors-insurance.
This article was produced by the R&I Brand Studio, a unit of the advertising department of Risk & Insurance, in collaboration with AXA XL. The editorial staff of Risk & Insurance had no role in its preparation.