Workplace Safety Trends
Evolving Technology Protects Workers ‘24/7’
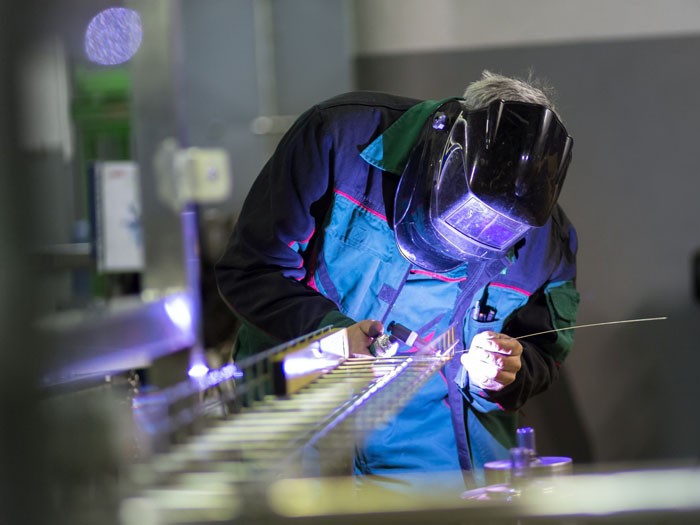
A worker in a high risk area gets an alert: three feet away from him and one foot above there is a brace that is about to give way, putting the worker and his colleagues at risk. Because he received the information when he did, the workers were able to take steps to protect themselves and avoid damage to the facility.
The technology isn’t necessarily new. But what is new is the connectivity of the worker to the Internet with data passing immediately to supervisors who can analyze the information and provide feedback back to the worker.
It’s being called ‘the next industrial revolution.’ It’s enabled by IoT — the Internet of Things. And it’s saving companies an average $200,000 to $300,000, depending on the size of the facility.
“This convergence of industrial systems that exist and marrying them with advanced computer capabilities, low cost sensors — we have a new wave of going back into the industrial settings and improving efficiencies for the operation but also worker safety,” said Bridget Karlin, managing director of the IoT Strategy and Office in the Internet of Things Group at Intel. “That’s essentially what’s happening.”
Intel has partnered with Honeywell to create a personal connected safety solution for industrial workers. The prototype was recently introduced at an annual showcase demonstrating innovative IoT hardware and software.
How It Works
The Honeywell Connected Worker solution begins with ‘connecting’ a worker from head to toe with various WiFi and communication technologies. Basically, the worker’s standard operating gear is equipped with sensors and other technologies.
“They are being integrated into everyday tools the industrial worker already uses and is now being enabled with these wearable technologies and becoming part of it,” Karlin explained. “The old hard hat becomes a smart helmet; the vest you wear to climb a pole is outfitted with technology, helping you stay safer.”
Smart watches worn by the worker can capture pulse and heart rate information. A ‘smart’ body activity belt includes various sensors, including ones that can understand gestures.
“So [the worker] could wave his arm in a certain way, spell a letter with his arm, and it could mean ‘man down,’” she said. “We have these wearable technologies that are basically collecting data that is being transmitted through a mobile hub he is also wearing. Your phone can act as a mobile hub … collecting data, sending it to the Internet, and that data is getting analyzed for things like what the worker is doing.”
Depending on the industry and type of facility, the sensors could be incorporated in self-contained breathing apparatus and a heart rate monitor. Information about the worker’s heart rate, posture, motion, and potential exposure to toxic gas can be transmitted.
“We are connecting different devices and getting the data into actionable form, so the worker is protected 24/7,” said Prabhu Soundarrajan, Global Business Development director at Honeywell analytics. “When a worker is doing jobs with varying levels of risk, we really use technology to put more eyes on the problem. Somebody in a control room can see if there is a panic alarm, a gas alarm, or an injury … We are able to really help mitigate a lot of the risk for the worker.”
Adapters
Honeywell plans to begin using the system for gas inspectors in the near future. Beyond that, the company believes it can be used just about anywhere.
“We really see this market evolving and connectivity driving real time data and providing safety compliance and productivity,” Soundarrajan said. According to the Gartner Group, network-connected devices will soar to 26 billion by 2020.
Factory workers for example, could don the wearable devices to enable bidirectional data between the worker and supervisor. “So if he is going to bring a line down, what else should he be looking at?” Karlin said. “Or, ‘you were supposed to do this particular repair, but it doesn’t need it.’”
Mine workers, health and safety workers, even office workers could take advantage of the technology, the companies say. “Even a worker for Amazon who is fulfilling shipments,” Karlin said.
Costs
While neither company would release specific cost figures, officials said they are trying to make it affordable. “We’ve changed our model to be extremely scalable,” Soundarrajan said. “Our goal is to really make it easy to adopt in terms of switching costs … If the technology is too expensive, they won’t use it.”
Soundarrajan said the system can be a huge cost saver for companies. “We’ve done some analysis in the market,” he said. “Each [savings] at an average sized plant [would be] $200,000 to $300,000, depending on the plant site.
Some companies may find they don’t need to make too many changes to use the system. “Many of these industrial settings already have sensors in place and haven’t really utilized the data available,” Karlin said. “Now we can send the data from the worker, so you have a fusion of data and now we are taking advantage of things already in place.”