Employers Embrace Safety Tech to Enhance Workplace
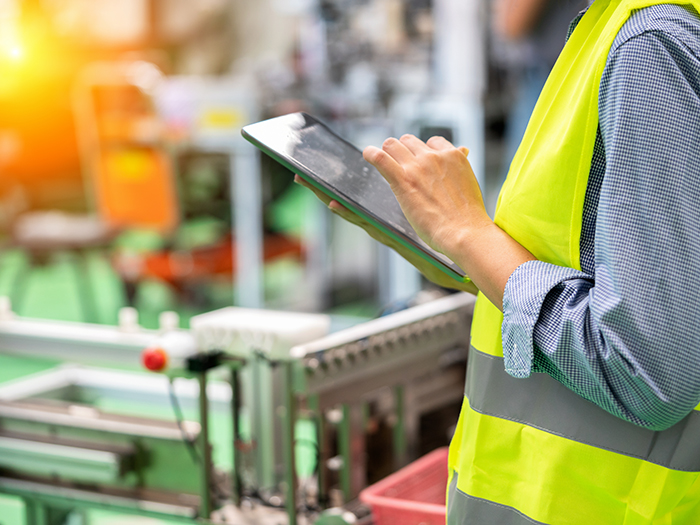
The role of safety technology in today’s is top of mind for workers’ compensation stakeholders, according to a recent report by the National Council on Compensation Insurance (NCCI). As part of its series on the current state of workplace safety technology adoption, NCCI interviewed representatives from three employers at different stages of implementing safety technologies, such as wearable devices.
Implementing Safety Technologies
Two of the employers interviewed for this article first learned about safety technologies through their workers’ compensation insurance providers. The insurers invited the companies to participate in pilot projects to test out the technologies, with the insurers funding at least part of the costs.
Another employer shared that they make it a practice to try out a different safety innovation tool or technology every year or two. “This employer’s goal was to be proactive rather than reactive in addressing workplace hazards,” per NCCI.
Obstacles to Implementation and Solutions
While safety technologies offer significant potential benefits, employers do face some obstacles in implementing them. Managing and acting on the large volume of data collected by the technologies can be challenging. One employer that piloted wearable devices met regularly with the technology provider and workers’ comp insurer to review the data and determine how to most effectively utilize the information.
Employee privacy concerns are another hurdle. Workers may be skeptical at first about how data from wearable devices and other monitoring technologies will be used.
“Employees were concerned about whether they would get in trouble,” according to NCCI. Education, transparency, and an open, honest company culture proved key in alleviating these concerns, the report noted.
One employer utilizing computer vision technology, a field of artificial intelligence that allows computers to extract information or data from photos or video, took the approach of showing video clips to individual employees involved, rather than the entire workforce, and used the feedback for training rather than discipline. “It’s important to do it in a caring manner and present the video clips the right way,” the employer noted.
While technology providers and insurers have pointed to product costs as a potential barrier to widespread adoption, two of the three employers interviewed did not see cost as a major obstacle. One employer shared that if the technology could prevent just one back strain, it “paid for itself.” Another noted that while cost was a consideration, the benefits—such as not needing a safety manager at every location—helped offset the expense.
Monitoring Change and Results
The employers interviewed reported that the safety technologies they implemented had a clear positive impact in their workplaces. By constantly monitoring the data and feedback from these systems, they were able to identify issues and make changes to improve safety, according to the report.
One manufacturer utilizing wearable devices meets daily to review the data, as well as monthly with the technology provider’s experts.
“The data from the wearable devices show ergonomic issues, such as the need for a lift table or tool; and body motion (push/pull injuries) so the employer can change the work process or the employee can change their process or alleviate stress on their body in other ways,” the NCCI reported. This led to over 335 “good catches” with 82% mitigated and a 60% reduction in workers’ compensation costs from 2021-2023.
Beyond the direct safety improvements, the employers noted additional positive business impacts from adopting these technologies, according to the report. These included fewer hours of lost time, trip hazards, and damaged pallets; cleaner and more efficient work areas; enhanced employee morale; improved facility security by ensuring doors and gates are properly closed; and increased efficiency and productivity overall.
Vision for the Future
While employers are already seeing positive results from implementing new safety technologies, they have a clear vision for how these solutions could be enhanced in the future to provide even greater workplace safety, according to the NCCI.
One desired feature is the ability to monitor a wider range of potentially hazardous exposures. For example, a manufacturing company currently utilizing wearables would like to see future versions flag vibrations impacting workers’ arms and bodies. They are also interested in monitoring additional exposures during processes like crimping and cutting that are not captured by current wearable devices.
In industries like warehousing and logistics, there is interest in leveraging technologies such as computer vision to evaluate overall proximity of employees. This type of monitoring could help eliminate workplace violence incidents by allowing situations to be de-escalated before they turn dangerous.
Automation is another area ripe for future advances. A freezer storage company, also using computer vision, uses robots operating in their freezers and forklifts that can drive themselves. However, their primary interest is in any new technology that can foster a safer work environment for employees.
So are these safety technologies true game-changers? Employers have differing opinions.
“100% game-changer—especially for a department of one!” said one company. Another finds the 24/7 worksite monitoring enabled by their solution to be revolutionary for their operations.
However, one employer notes that while the technology has game-changing potential, it is not quite there yet. They point out that workplace safety is complex, with many contributing factors beyond just technological solutions. Despite this, the rapid advances in safety technology and the ambitious future plans of employers suggest these solutions will only become more impactful moving forward.
Access the full report from NCCI here. &