Beyond Mere Compliance: How to Work with OSHA to Keep Workers Safe in 2023
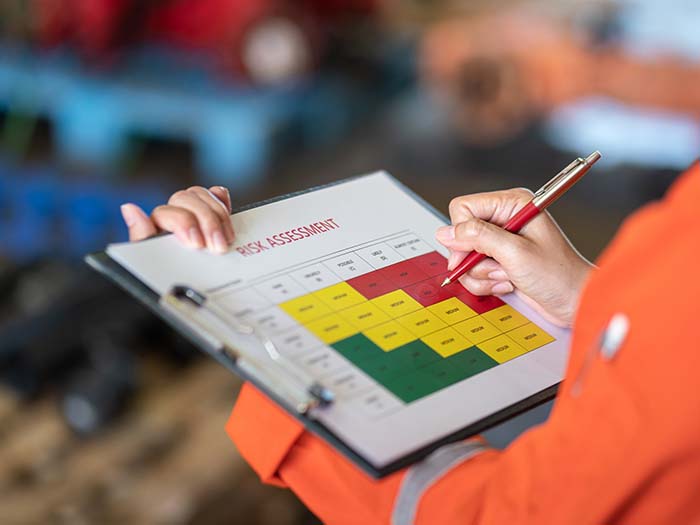
Many U.S. management leaders wrapped up 2022 on calls with their insurance brokers preparing them to see more of OSHA in the year ahead.
Following the Biden Administration’s March 2022 release of the FY 2023 budget proposal, subcommittees with authority over the Department of Labor met to review recommendations for bolstering OSHA’s budget by upwards of $100 million.
The proposed funding increases were for additional compliance officers, whistleblower investigators and standards directorate responsible for standard setting in both general industry and construction. Although this news may have caused concern among some employers, a stronger OSHA can help many businesses improve their safety conditions.
Improve OSHA, Improve Safety
Historically, “OSHA has received a reputation for being more on the ‘gotcha’ side of things, as opposed to on the helpful side of things,” said Matt Zender, SVP of workers’ compensation strategy, AmTrust.
Many OSHA resources are especially helpful for small businesses. For employers with 250 employees or less, OSHA operates and funds a free safety and health consultation service.
“This program will basically provide a free OSHA visit,” said Richard Fairfax, a principal workplace safety consultant with the National Safety Council. “The small employer’s obligation is to correct any serious violations. No citations or penalties are associated with the consultation visit.”
But worker advocacy groups such as the National Council for Occupational Safety and Health (National COSH) wanted OSHA to get a major funding boost to lessen critical hiring deficiencies: At the start of the pandemic, OSHA had only 750 inspectors — the lowest number in its 51-year history.
“When COVID-19 tore through our workplaces in 2020, OSHA’s response was totally inadequate,” said Jessica E. Martinez, co-executive director of National COSH. “Weak guidance, not enough inspections, no answers to repeated complaints from workers. We can’t let that happen again.”
“Graham has a philosophy that ‘culture beats compliance’ … Our goal for our clients is all employees working safely all the time. The most important thing is that workers go home at the end of the day.” — Mark Troxell, senior vice president, Graham Company
OSHA Initiatives
OSHA’s national emphasis programs (NEPs) are an example of a critical resource that helps keep workers safe in the face of evolving public health and environmental risks.
“OSHA establishes the NEPs based on injury and illness data, reports of health hazards from NIOSH, emerging new hazards, and inspection and citation history,” Fairfax said. “The NEPs are designed to be established rather quickly and direct enforcement resources to the hazard or the particular industry.” There are normally 12 to 14 NEPs in operation, including the NEP launched in April 2022 to prevent heat illness.
Local emphasis programs (LEPs) target OSHA inspections in the same manner as NEPs, Fairfax added, but “there are more than 140 of these programs. NEPs and LEPs are perhaps OSHA’s main method of targeting inspections at the program level.”
Whether in-person or online, OSHA’s tools and data can help companies benchmark themselves against industry peers, Zender said.
“OSHA’s webpage is a good resource,” added Natalie Hahlen, director of environmental health and safety for 2022 Teddy Award-winner Quad. She often looks to OSHA for regulatory updates and to monitor injury concerns among manufacturers.
What Businesses Should Focus On
Keeping abreast of regulations can be challenging, as OSHA and local entities frequently change their requirements. However, there’s much that management teams can do to keep workers safe and remain in compliance, said Mark Troxell, SVP, Graham Company.
While lagging indicators such as OSHA’s DART, TRIR and LTIR rates are valuable, “there are many leading indicators that can be used to measure the success of your safety efforts,” Troxell said. “It’s important to measure leading indicators through self-inspection incidents and near-miss reviews, time taken to address corrective actions and noncompliance issues observed on job sites, etc.”
First, safety managers and directors can conduct in-house evaluations and inspections, Troxell said: “Know what you currently have in your program and know what you don’t have. In other words, be honest with yourself.”
Look for ways to simplify compliance. “There’s a lot of good stuff out there,” he said, citing recordkeeping software and hazard communication programs as examples.
“Be prepared to make changes in your program or controls to address exposures present. If you’re self-evaluating, and doing it honestly, you want to move your program forward. Often, this involves looking at your existing safety culture,” Troxell said.
Have a Plan
Businesses should look to OSHA’s LEPs and NEPs to ensure they have the proper controls in place for common workplace safety exposures, he added. “Understand what the standard says and what the regulatory authorities actually expect or require of you.”
Troxell said local associations can provide updates on proposed OSHA changes. “It’s good to talk to others in the industry who have common exposures and issues to see what they’re doing,” Troxell said. “Hopefully, we all can learn together.
“After you get everything in place, make sure that you’re following up and self-auditing,” Troxell added. “Graham has a philosophy that ‘culture beats compliance’ … Our goal for our clients is all employees working safely all the time.” The most important thing, Troxell said, “is that workers go home at the end of the day.”
OSHA’s $632 million allotment in the $1.7 trillion omnibus bill passed in late 2022 is much less than the $712 million that worker safety advocates wanted in FY 2023.
That said, with a similar prior budget increase, OSHA conducted approximately 7,000 more inspections in 2022 than 2021 and hired more than 400 new employees, 250 inspectors and 15 whistleblower inspectors.
But workplace fatalities are still increasing, which is why advocates like Martinez’s co-executive director, Marcy Goldstein-Gelb, find OSHA’s 3% budget increase inadequate: “We hear constantly from workers who are facing hazardous conditions but can’t get an effective response. It just doesn’t make any sense to starve the one part of the federal government that is supposed to protect the safety of more than 160 million workers.” &