Risk Report: Manufacturing
Struggling With Safety Rules
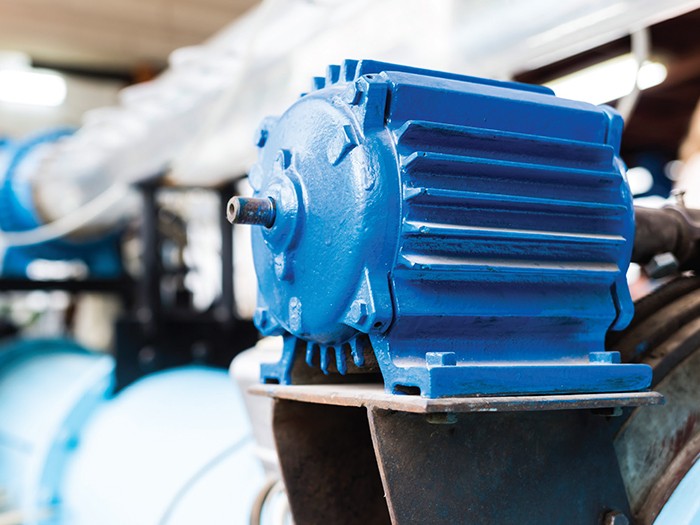
Manufacturers that have operations in one or more states have the complex task of complying with either state or federal safety and health standards — and the provisions are not always in alignment.
Failure to do so means they run the risk of being hit with hefty fines totaling hundreds of thousands — or even millions — of dollars.
The U.S. Occupational Safety and Health Administration (OSHA) requires all companies to meet its regulations as a minimum. However, firms that have operations in one of the 26 states that have adopted their own occupational safety and health rules must also adhere to each state’s rules.
State-run programs are required to meet minimum federal requirements, but often they are more stringent. In many cases, companies operate in multiple states, so they have to subscribe to a range of different standards for each state.
Employers are required only to comply with the state-run program; if there is no state program, they must comply with the federal rules.
To compound this, according to industry sources, federal OSHA has just increased the maximum penalty by nearly 80 percent for failure to comply with its standards, meaning that companies that fail could be hit with a fine of $125,000 or higher for a serious violation.
And with thousands of cases of workplace injuries believed to be unreported every year, federal OSHA is now tightening the net on willful and repeat offenders.
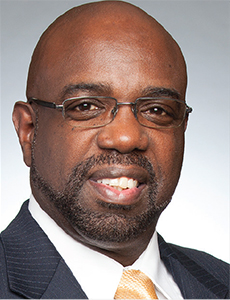
Robert Cartwright, safety and health manager, Bridgestone Retail Operations LLC
“State plan standards are often higher or exceed those of federal OSHA,” said Robert Cartwright, safety and health manager for Bridgestone Retail Operations LLC and a board director of RIMS.
“With fire safety, for example, in states like California, where they have had a certain violation or frequency and severity of violation, the state may decide to apply their own set of standards that are tougher than the federal OSHA.
“In my experience, in those particular cases, the fines tend to be higher and the citations more detailed than they would be from the federal authority.”
State vs. Federal OSHA
David Carlson, Marsh’s U.S. manufacturing and automobile practice leader, said that state plans are often more stringent in terms of enforcement protocols and the composition of their hazard communication programs such as labeling requirements, exposure limits and types of chemical used.
For example, he said, California created a standard specifically focused on reducing and eliminating hazardous chemicals from the workplace. It has significantly tightened up exposure limits and the quantities that can be stored.
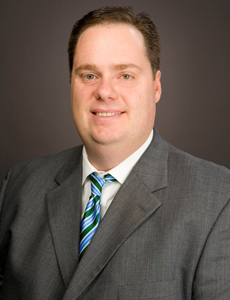
Dave Barry, senior vice president and national director of casualty risk control, Willis Towers Watson
Dave Barry, senior vice president and national director of casualty risk control at Willis Towers Watson’s risk control and claims advocacy practice, said California’s state plan requires companies to implement a written injury and illness prevention plan, while federal OSHA does not.
Sometimes, he said, the U.S. regulations will be revised to match state rules, such as the requirement for reporting an amputation, hospitalization or loss of an eye within 24 hours, which had already been in force in states like California for several years.
“The state programs typically focus their efforts on the specific industries in their state, for example if they do a lot of agriculture, whereas federal OSHA standards are not necessarily geared toward one particular industry,” he said.
He said that regulations often vary widely from state to state.
On the other hand, Mike Heembrock, vice president and executive specialist, risk engineering at Chubb, said that states often fall short of federal OSHA enforcement performance in terms of inspections and fines because of staffing and resource limitations due to budget constraints.
“In general, because of the relatively low salary and operating budgets, states have struggled to recruit new inspectors and often they don’t have as much experience as federal inspectors, so it’s been difficult for them to meet federal OSHA performance criteria,” he said.
Risks for Manufacturers
Carlson said that the biggest risk for manufacturers operating in multiple states is to understand how to comply with different state and federal standards and record-keeping requirements.
“If you have operations, say, in California, Michigan, Oregon or Washington, those
all have their own state plan programs that you need to be aware of and comply with, not to mention the administrative burden and costs associated with complying with federal OSHA in other states where they may operate,” he said.
“That’s a challenge for not only a large manufacturer like Ford or GM, but also for smaller businesses with operations across the U.S.”
Carlson said that oftentimes companies become preoccupied with emerging risks such as cyber and overlook the broader risk of their employees’ health and safety.
“At the end of the day, the largest variable cost of risk for most manufacturers is still the workers’ compensation and employee benefits programs,” he said.
“The problem is that too many employers look at it simply as the cost of doing business; however if they focused on it, that’s the area where they could reduce claims and financially protect their balance sheet.”
Fines and Penalties
U.S. OSHA raised its penalties for the first time in 25 years, by 78 percent last November.
The maximum fine for a serious violation rose from $7,000 to $12,500, and the maximum willful or repeat violation increased from $70,000 to $125,000. State plans are expected to follow suit, taking effect from August this year.
And from now on, the penalties will be increased every year.
“I think we are going to see a lot more of these types of changes as the current administration leaves office,” said Barry.
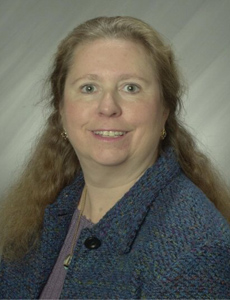
Adele Abrams, Law Office of Adele L. Abrams
“It’s been 25 years since the fee schedule has been increased and now it will be increasing every year, so I think we are going to see more additional requirements along these lines come into force.”
The maximum penalty per citation can also be higher if it is an egregious violation, said Adele Abrams, whose law practice is based in Beltsville, Md.
“If you have, for example, 10 employees working on a conveyor system in your facility and it doesn’t have adequate guards in place to protect them from injury, federal OSHA would usually issue a single citation with a maximum penalty of $70,000,” she said.
“However, if all of a sudden they decided it was an egregious violation, because there are 10 workers involved, you could be fined up to $700,000, and you would be put into a ‘Severe Violator Enforcement Program’ for at least three years.”
Christine Sullivan, vice president of risk control services at Lockton, said manufacturers should “avail themselves of the relevant programs that federal OSHA provides.”
“There are a lot of programs and resources out there than can help a risk manager to identify the pitfalls and build a thorough and reliable safety program.” &