Injury Prevention
Time to Prioritize Proactive Ergonomics
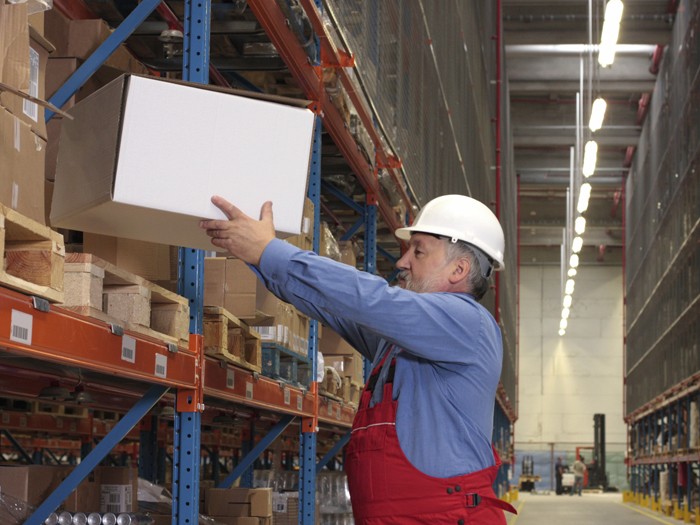
According to a recent benchmarking study conducted by Aon, which collected data from 150 companies who attended either the ASSE annual Safety conference or the Michigan Safety Conference this year, 27 percent of companies have no one designated to handle ergonomics in the workplace, and only 13 percent were conducting formal risk assessments of their ergonomic exposures.
“That was a surprising result, because when you look at our casualty analytics, ergonomic injuries are up in the top two or three in terms of severity and cost,” said Scott Smith, director of ergonomics at Aon.
Ergonomics is frequently overlooked by executives, and there a few reasons why. The lagging indicators that many organizations use to track frequency, type and cost of on-the-job injuries often fail to show the connection between those injuries and their effect on productivity. The safety metrics are isolated.
As a result, improving safety is largely seen as a way to save expenses, rather than as an integral part of an overall strategy to improve efficiency and boost performance.
“Ergonomic injuries are up in the top two or three in terms of severity and cost.” — Scott Smith, Director of Ergonomics, Aon
Lagging data can also be incongruent with workers’ comp and health care data, which often exist in separate silos. Musculoskeletal workers’ comp claims illustrate that disconnect. Such soft tissue injuries can appear to have nothing to do with safety because the safety team is focused on tracking OSHA-recordable events.
A shoulder strain that occurs after repeatedly reaching too far for a tool or a keyboard, for example, would not fall into that category, and thus may be overlooked by safety metrics.
“Most companies haven’t gone through the process of looking at workers’ comp and health care data together to show how injuries are related and how a more comprehensive approach can bring costs down for both,” said Rick Spencer, Head of Prevention and Optimization at Briotix, an ergonomics and injury prevention consulting firm. “Execs need to see that data to support a new initiative.”
Without these pieces fitting together to show the whole picture, senior decision-makers are unlikely to be convinced that ergonomics plays a central role in reducing injury, cutting costs, and improving operational performance.
Reactive vs. Proactive Approach
As a result, many companies take a reactive approach to ergonomics injuries, only evaluating or changing the ergonomic design of a workspace after an employee gets hurt.
This approach “misses the boat,” Smith said. “You know where you’ve gone, but you have no idea where you’re going.”
To get C-suite support, safety professionals and risk managers have to pitch proactive ergonomics not as a safety initiative, but as a business tool that aligns with specific operational goals and metrics.
In manufacturing, for example, “they have metrics around improving throughput, reducing costs, reducing cycle times, and they have to meet those goals on a budget,” Smith said.
He described one medical device company that was spending almost $4 million per year in ergonomics injuries across 27 plants.
“We discussed a strategy to roll out a proactive ergonomics program. Not as a tool to improve safety metrics, but as a tool to support manufacturing metrics. They wanted a 25 percent reduction in cycle time, 50 percent reduction in quality issues, a 20 percent reduction in space, and improved throughput by 20 percent. Ultimately, we were able to show $5.7 million in improvement related to these metrics, just by improving ergonomics.”
Even in an office environment, proactive ergonomics helps companies improve talent recruitment and retention, especially among younger employees just entering the workforce.
One example of a proactive program for an office is a web-based app that asks workers to describe and evaluate their work spaces. The app will identify possible ergonomic hazards and make suggestions to eliminate them.
“A lot of companies are nervous about this, because they think it means they’ll have to go out and buy a new chair for everyone, but often the changes are much simpler than that and cost nothing,” Spencer said. The recommendations include things like adjusting the height of a chair or moving commonly used items closer to avoid over-reaching.
“Typically, safety programs have been a one-way conversation, with employers broadcasting the message ‘safety is our #1 priority.’ Millennials want to see employers back that up.” — Rick Spencer, head of prevention and optimization, Briotix
Additionally, these programs improve employee satisfaction because they engage workers and empower them to make changes to their environment. They go a bit further than the tried-and-true “suggestion box,” Spencer said, because they provide instant feedback.
“This is especially important for retaining millennials. They want to have their voices heard, and they want feedback. They also value their work environment almost as highly as they do compensation,” he said.
“If they’re not happy with where they work, they’ll leave. They won’t put up with waiting around to see if they get hurt.”
Millennials will constitute the majority of the workforce by 2020, so employers need to focus on additional ways to engage with them.
“Typically, safety programs have been a one-way conversation, with employers broadcasting the message ‘safety is our #1 priority,’ ” Spencer said. “Millennials want to see employers back that up.”
Apps also have the added feature of being interactive and fun. Smith said that social media platforms can be a useful tool for soliciting feedback and measuring sentiment around safety programs, which risk managers can use to make adjustments.
“We have to leverage technology to get ahead of ergonomic injury risk and to engage workers early,” Spencer said. “It all comes down to recognizing that your people are your greatest asset, and treating them as such.”