2016 Teddy Award Winner
The Family That’s Safe Together
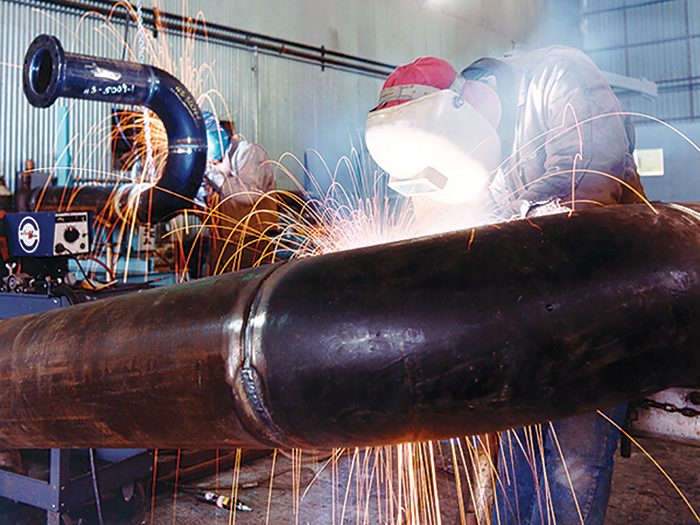
From a safety and workers’ comp perspective, the construction industry is one of the most daunting of all industries. The numbers say it best. One in 10 construction workers is injured every year, according to OSHA, and over the course of a 45-year career, a construction worker has a 1 in 200 chance of dying. Sobering odds.
One company beating those odds is Harder Mechanical Contractors, a 2016 Teddy Award winner.
Portland, Ore.-based Harder Mechanical specializes in process piping fabrication and installation, equipment installation, commercial HVAC piping and plumbing, instrumentation and controls, civil and poured-in-place concrete work and structural steel erection services.
The size of the company’s workforce varies, ranging from around 2,000 to more than 3,000 employees, depending upon the number of projects the company has in the works. Having that kind of revolving-door operation can be a major stumbling block for a safety program. But it has actually made the company double down on its efforts to create a safety culture that can thrive even as workers come and go.
“It’s a never-ending battle,” said Jennifer Massey, the company’s corporate director of safety and health and claims management. “Every day we have to reinforce it.”
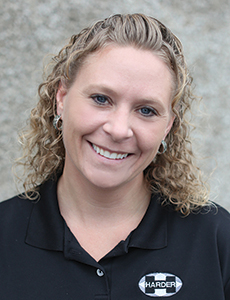
Jennifer Massey, corporate director of safety and health and claims management, Harder Mechanical Contractors
It’s a battle they’re winning. The company’s injury frequency plunged from 71 to 18 in the past four years, and its total incurred cost per claim dropped from $21,322 in 2011 to $683 in 2015.
“We have a team that is aligned and focused to prevent injuries at the jobsite,” said company President Dustin Harder. “Our senior leaders are trained to support our crews and a lot of attention is put on the boots on the ground. Our field foremen are the first line of defense to preventing injuries and properly managing the ones that do occur.”
“Every person in the company, from the president to the apprentice, is deeply committed to the goal of achieving zero-injuries,” agreed the company’s general counsel and risk manager, Bill Murphy.
Results like that take diligence. Massey’s team is constantly on top of its leading and lagging indicators, working to spot any sign that the company’s safety efforts may need a course-correct.
When the team became concerned that workers were suffering hand injuries despite wearing gloves, it set out to find out why.
“The problem was, we just weren’t helping them to understand that they needed to wear the right gloves for the job they were doing, or to stop and change [gloves] as the conditions change,” said Massey.
With worker input, the team created a colorful quick-reference 4-by-8-foot glove matrix banner, matching images of glove types to specific jobs and tasks.
“We don’t want to just impose something upon the people out there in the field — they’re the ones turning the wrenches, and know how to do their jobs safely. We need to get their input so they own it,” she said.
The outcome was even better than expected — a rapid 60 percent reduction in hand injuries.
Getting to Zero
Harder Mechanical’s lost-time accident rate is enviable: Zero. The company just reached a remarkable 16 million man hours without a lost-time accident.
“That one is actually our easiest situation to deal with,” said Massey, well aware of how surprising that sounds. The key, she said, is an environment of trust. Workers readily partner with the company to make zero lost-time happen.
Employee pay scales are negotiated under collective bargaining agreements for each state jurisdiction and craft. If somebody is off work and getting TTD payments, said Massey, “they are severely affected” in terms of salary, health and welfare benefits for their families, and pension credit hours.
That’s a heavy burden to bear. Harder Mechanical makes sure that every employee understands there’s another option.
“We effectively communicate with them that … you can partner with us, and get your doctor involved, and all of us come together and agree that we’re going to keep you working no matter what. … Which would you choose if you were an injured worker?”
In the short-term, Massey’s team provides online training platforms. Recovering workers are brought to a warehouse location, where it’s easiest to accommodate restrictions safely. Treating physicians are highly cooperative because they understand that workers’ recoveries will not be compromised, and are inclined to follow their patients’ wishes.
“I tell [workers], you have to advocate for yourself and tell your doctor, ‘No, this is what I am doing; this is how the company and I are partnering.’ ”
In 2014, a steamfitter nearing retirement suffered a crushed leg, and nearly lost his foot. Despite multiple surgeries, he was able to utilize the online training platforms until he could return to modified duty at the warehouse.
The employee couldn’t return to his job in the same capacity, so Massey’s team brought in a vocational specialist to help design a permanent job description for him.
With assistance from the state’s preferred worker program, Harder provided numerous accommodations, including special shoes, rolling stools that allow him to rest his leg, a motorized scooter and a golf cart which he uses to travel between buildings.
“We don’t want to just impose something upon the people out there in the field — they’re the ones turning the wrenches, and know how to do their jobs safely. We need to get their input so they own it.” — Jennifer Massey, corporate director of safety and health and claims management, Harder Mechanical Contractors
Throughout the entire journey, he never had to worry about whether he’d be able to provide for his family. That allowed him to focus on his recovery. Eliminating that anxiety has a major impact on outcomes, Massey said.
“Our employees are not affected adversely, financially, so they’re focusing on getting better because they’re not stressed out about how they’re going to pay their bills, or how they’re going to have medical benefits for their family,” she said.
The Human Connection
One important feature of Harder Mechanical’s safety culture is how the company communicates with employees, reminding them why safety matters in the first place, especially in their lives outside of work.
That comes into play with safety commitment letters — letters that workers are asked to write to their families, making a personal promise to work safely.
It’s a tool so powerful that the company only uses it when circumstances warrant a wake-up call.
“We use it when we feel like we’re definitely trending the wrong way and we have to take prompt corrective action to turn the train around before something happens,” Massey said.
The same principle is applied in a lighter fashion in the company’s newsletter. That features a retiree profile in each issue that details the joys of a retirement they worked so hard for.
For Massey, getting employees safely to those golden years is personal.
“Coming up through, with my dad in the shipyard, [I knew] a lot of my dad’s colleagues who passed away from asbestosis, or they were totally broken down … their quality of life was not what it should be. … People who work hard, they deserve to enjoy the rest of their lives after working.”
Massey said the commitment to protecting every Harder Mechanical employee runs from the top down.
“For me safety is a value that we will never sacrifice,” said Harder. “I have worked personally with many of the guys within our company; they are an extension of my family, the Harder family. If one of them were to get hurt it’s like a family member gets hurt.”
“The company’s message and safety programs are focused on every worker being able to go home to their families at night in the same condition as when they left for work in the morning,” said Murphy. “I have always been impressed with the company’s consistent approach in all aspects of its business: ‘Do the right thing.’ ” &
_______________________________________________________
Read more about the 2016 Teddy Award winners:
Bringing Focus to Broad Challenges: Target brings home a 2016 Teddy Award for serving as an advocate for its workers, pre- and post-injury, across each of its many operations.
The Road to Success: Accountability and collaboration turned Hampton Roads Transit’s legacy workers’ compensation program into a triumph.
Improve the Well-Being of Every Life: Excela Health changed the way it treated injuries and took a proactive approach to safety, drastically reducing workers’ comp claims and costs.
The Family That’s Safe Together: An unwavering commitment to zero lost time is just one way that Harder Mechanical Contractors protects the lives and livelihoods of its workers.
More coverage of the 2016 Teddy Awards:
Recognizing Excellence: The judges of the 2016 Teddy Awards reflect on what they learned, and on the value of awards programs in the workers’ comp space.
Fit for Duty: 2013 Teddy Winner Miami-Dade County Public Schools is managing comorbid risk factors by getting employees excited about healthy living.
Saving Time and Money: Applying Lean Six Sigma to its workers’ comp processes earned Atlantic Health a Teddy Award Honorable Mention.
Caring for the Caregivers: Adventist Health Central Valley Network is achieving stellar results by targeting its toughest challenges.
Advocating for Injured Workers: By helping employees navigate through the workers’ comp system, Cottage Health decreased lost work days by 80 percent.
A Matter of Trust: St. Luke’s workers’ comp program is built upon relationships and a commitment to care for those who care for patients.
Keeping the Results Flowing: R&I recognizes the Metropolitan Water Reclamation District of Greater Chicago for a commonsense approach that’s netting continuous improvement.